.jpg)
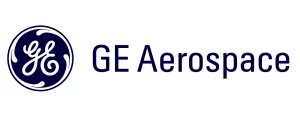
GE AEROSPACE
See us at MSPO 2025 · Booth: B06
GE Aerospace is a world-leading provider of jet and turboprop engines, components and integrated systems for commercial, military, business and general aviation aircraft. At GE Aerospace, we believe the world works better when it flies.
Cincinnati, Ohio, United States
Aerospace, Defense & Security
Products & Services
People
Other
About
Connect with us at
Products & Services
GE's F110: The Engine of Choice for Today's Front-Line Missions
GE Aerospace
Powering front-line fighters globally and backed by a continuous infusion of new technology, the F110 remains the engine of choice around the world.
Military Engines
GE Aerospace
Building on an unsurpassed legacy of success, GE continues to execute on bold technical initiatives to ensure even more demonstrable support to the warfighter and those in need of humanitarian relief.
Military Systems
GE Aerospace
GE Aviation's Systems business is equipping militaries with the solutions needed to succeed. As a leading supplier of integrated systems and technologies for combat aircraft, military transport, helicopters, land vehicles and unmanned aerial vehicles (UAVs), GE is enabling armed forces around the world to improve reliability and enhance operational performance.
GE's Passport engine
GE Aerospace
Discover why GE's Passport engine is B-52 ready.
GE's T901 engine is ready for the future of the US Army rotorcraft aviation
GE Aerospace
GE's T901 Engine for ITEPA test cell is not a combat mission. In combat, there is no time for an unproven design. With more than 100 million flight hours of ...
Military Services
GE Aerospace
From parts supply to total logistics support, GE has the right program to support your maintenance needs -- and keep more of your assets in their theater of operation. Our extensive maintenance management experience can maximize your engine and parts availability by improving procurement lead time and boosting shop productivity.
GE's CF34-10 for B-52
GE Aerospace
Fly through GE's CF34-10 engine to learn why it is ready to power the B-52 into the future.
People
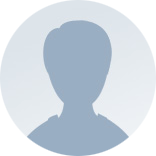
Ali Nettles
GE Aerospace
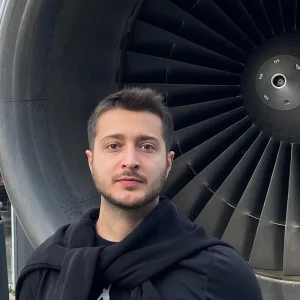
Alp Giray Karakoc
GE Aerospace
Aerospace Eng
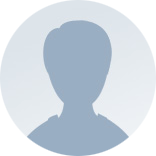
Andrea Paz
GE Aerospace
Gerente de compras
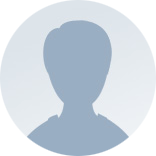
Bridget Harding-Williams
GE Aerospace
Trade Show Coordinator
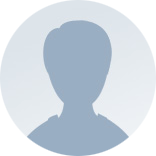
Cheol Park
GE Aerospace
Sales Director, North Asia Defense & Systems
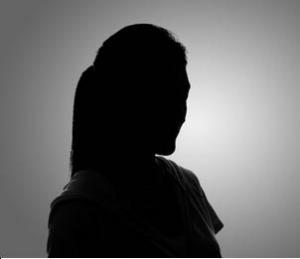
Emma Harrison
GE Aerospace
MSPO 2025
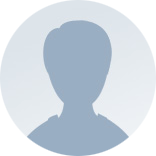
Jetzabel Perez Palacios
GE Aerospace
Gerente Senior
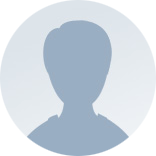
Josh Gregg
GE Aerospace
Airfoils Supplier Program Manager
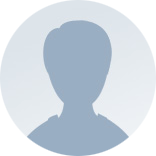
Maria Almada
GE Aerospace
Sr. Component Engineer
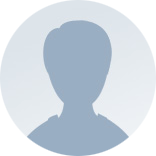
Mark Musheno
GE Aerospace
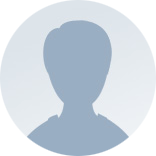
Nicola Withington
GE Aerospace
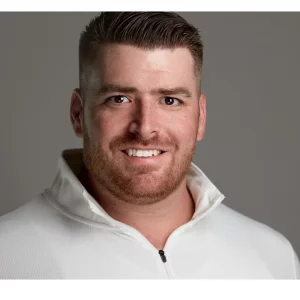
Ryan Forbes
GE Aerospace
Tradeshow/Event Manager
MSPO 2025
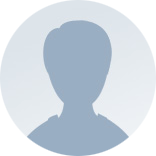
Ryan Forbes
GE Aerospace
Tradeshow Manager
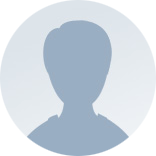
Steve Rogers
GE Aerospace
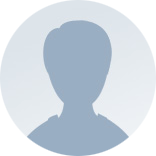
Sungkwon LEE
GE Aerospace
Sr. Global & Key Accounts Director
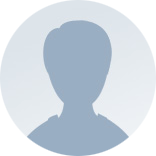
Thuy Nguyen
GE Aerospace
Government Engagement Director
Connect with us at
About
GE Aerospace’s military division is working on innovations today that will transform tomorrow’s missions. From the revolutionary Adaptive Cycle Engine (ACE), in conjunction with the Air Force Research Lab, to the T901 for the Army’s Improved Turbine Engine Program (ITEP), GE Aerospace’s next generation portfolio includes unprecedented speed, power, fuel efficiency and reduction in maintenance costs. These advancements will forever change the military’s approach to protecting freedom.
This ambition for building upon previous technology, knowledge and experience goes back to the Company’s first generation of engineers. GE rapidly grew its jet engines business thanks to the industrialization of the most produced combat engine, the J47, with more than 35,000 manufactured.
As the need for more power for the Century Series fighters, which would fly at more than twice the speed of sound, GE responded with one of the most important developments for the jet engine, the variable stator for its J79 turbojet engine. The movable stator vanes in the engine helped the compressor cope with the huge internal variations in airflow from takeoff to high supersonic speeds.
More than 17,000 J79s were built over 30 years, powering aircraft such as the F-104 Starfighter, F-4 Phantom II, RA-5C Vigilante, and B-58 Hustler. For the Convair 880/990 series airliner, the CJ805 derivative of the J79 engine marked GE's entry into the civil airline market.
Meanwhile, GE was busy a new gas turbine to transform helicopter capability. The 800-horsepower T58 turboshaft engine powered a Sikorsky HSS-1F in the U.S.'s first turbine-powered helicopter flight. That engine, which first ran in the 1950s, was the precursor of Lynn's small engine product line.
The 1950s and 1960s saw further advances. The J93 was developed to power the world’s largest, highest flying, and fastest bomber, the US Air Force’s experimental XB-70 Valkyrie. Six 28,800 lb thrust turbojets propelled the 500,000 lb demonstrator to three times the speed sound at an altitude of 74,000 feet. Technologies pioneered in the J93 are used in today’s military and commercial engines.
A major success of the period was the Lynn-manufactured J85 turbojet engine. Contracted by the USAF to build a low-cost air-combat fighter, Northrop built the F-5 Freedom Fighter around the GE J85 engine. The F-5 soon became the standard air defense aircraft for more than 30 nations. The J85 powers the US Air Force T-38 Talon supersonic pilot trainer.
GE introduced the T64 free-turbine turboshaft/turboprop engine in 1964, featuring technical innovations such as corrosion resistant and high-temperature coatings that contributed to the development of very heavy lift helicopters. The T64 was used on the Sikorsky CH-53 Sea Stallion family of helicopters that serve the US Navy, U.S. Marine Corps and several international militaries.
When the U.S. Navy needed a durable and efficient engine to power the Lockheed S-3 Viking for carrier based anti-submarine warfare, GE responded with the TF34 high bypass engine. The TF34 was also selected by the U.S. Air Force to power the A-10 Thunderbolt II close air support aircraft.
Advances in compressor, combustor and turbine knowledge in the 1960s led to the decision to propose a more compact core engine with a single-stage turbine and only two bearing areas versus three, resulting in the GE F101 engine, selected for the U.S. Air Force's B-1 bomber.
In the early 1970s, the Army turned to GE for an improved turboshaft engine to power its new generation of helicopters. The result was the legendary T700. Capitalizing on the lessons of the Vietnam War, the T700 provided the Army exceptionally reliable power built using a revolutionary modular architecture. The modular T700 was designed for field maintainability to drive down costs and improve Army helicopter readiness rates. Over the ensuing decades, multiple advanced technology upgrades were introduced for the T700. Also, the T700-derived, CT7 turboshaft and turboprop engine family was introduced for the commercial market. More than 25,000 T700/CT7 engines have been delivered. Since their introduction more than 40 years ago, the T700 and CT7 variants continue to establish new applications as one of the among popular turboshaft and turboprop engine families in aviation history.
The role of GE military engines continued to grow during the defense buildup of the 1980s. In 1984, the USAF selected GE's highly reliable F110 engine, based on the F101 design, for the F-16C/D fighter aircraft, initiating "The Great Engine War"- an intense, competition between GE and rival Pratt & Whitney. The F110 now powers the majority of USAF F-16C/Ds. The F110 also powers F-16s worldwide, having been selected by Israel, Greece, Turkey, Egypt, Bahrain, United Arab Emirates, Chile and Oman. In addition, the F110 powers Japan's single-engine F-2 fighter and the export versions of the F-15 Eagle operated by Korea, Saudi Arabia and Singapore. From the late 1980s through 2006, the US Navy operated an upgraded version of the F-14 Tomcat with the F110 engine. A derivative of the F110, the F118, powers the U.S. Air Force B-2 stealth bomber and U-2S high altitude reconnaissance aircraft.
Also in the 1980s, the F404 engine for the F/A-18 Hornet entered production. The F404 is the world's most ubiquitous fighter engine, with more than 3,700 powering 10 aircraft types worldwide. These include the Boeing F/A-18 Hornet, Saab JAS 39 Gripen, Korea’s T-50, India’s Tejas Mark I and the Lockheed Martin F-117 stealth fighter prior to its retirement in 2008.
GE is positioned to be a world leader in military propulsion well into the 21st century. The F414, the turbofan engine for the F/A-18E/F Super Hornet front-line strike fighter and EA-18G Growler electronic attack aircraft, produces 22,000 pounds of thrust. It is also the engine of choice for the JAS 39E Gripen Next Generation and HAL Tejas Mark II. GE Aerospace has the capability to increase F414 durability and thrust by as much as 25 percent.
GE first received funding to begin developing a competitive engine for the Joint Strike Fighter (JSF) in 1996 and ultimately teamed with Rolls Royce for the full-scale development contract. The team successfully completed Short Take Off, Vertical Landing (STOVL) testing on an F136 engine at the GE testing facility at Peebles, Ohio in 2008. Extensive ground testing of the F136, designed for all variants of the JSF aircraft for the Air Force, Navy and Marine Corps, included the first use of ceramic matric composites in GE-designed components and paved the way for expanded use of these revolutionary materials in GE’s next generation commercial engines and military engines.
Due to US Government fiscal challenges and DoD budget cuts, Congress made the decision in 2011 to discontinue funding development of the F136 and the program was cancelled after about 80% completion.
Building on the strength of its design capabilities for high performance combat aircraft engines, GE successfully completed testing the world’s first adaptive, three-stream engine in 2014 through the Adaptive Versatile Engine Technology (ADVENT) program with the United States Air Force Research Lab.
By the next decade, the adaptive cycle (also called variable cycle) engine could revolutionize jet fighters. The variable cycle engine alternatives between a high-thrust mode for maximum power and a high-efficiency mode for optimum fuel savings and greater aircraft range. In 2018, the USAF awarded to GE a $437 million contract to further advance adaptive-cycle engine technology, bolstering the company’s 11-year effort in this technology dating back to 2007.
GE’s next-generation military portfolio also includes the T901 turboshaft (downselected by the U.S. government in 2019) now under development, and also, the T408 turboshaft for heavy lift missions of the new Sikorsky CH-53 King Stallion for the U.S. Marine Corps. Capable of producing more than 7,500 shaft horsepower, the T408 combines breakthrough technologies, innovative cooling schemes and durability to deliver numerous mission-critical advantages in the world’s harshest operating environments.
The T901 is being designed as a replacement for the T700 engine powering existing Black Hawk and Apache helicopters through the U.S. Army’s Improved Turbine Engine Program (ITEP). Compared to the most advanced T700 engines in service, the T901 provides 25 percent better fuel economy, 35 percent lower acquisition and maintenance costs, 20 percent longer life and as much as 65 percent more power to weight.
GE Aerospace invests more than $1 billion each year in research and development, positioning the company to lead advancements in military propulsion for generations to come.
This ambition for building upon previous technology, knowledge and experience goes back to the Company’s first generation of engineers. GE rapidly grew its jet engines business thanks to the industrialization of the most produced combat engine, the J47, with more than 35,000 manufactured.
As the need for more power for the Century Series fighters, which would fly at more than twice the speed of sound, GE responded with one of the most important developments for the jet engine, the variable stator for its J79 turbojet engine. The movable stator vanes in the engine helped the compressor cope with the huge internal variations in airflow from takeoff to high supersonic speeds.
More than 17,000 J79s were built over 30 years, powering aircraft such as the F-104 Starfighter, F-4 Phantom II, RA-5C Vigilante, and B-58 Hustler. For the Convair 880/990 series airliner, the CJ805 derivative of the J79 engine marked GE's entry into the civil airline market.
Meanwhile, GE was busy a new gas turbine to transform helicopter capability. The 800-horsepower T58 turboshaft engine powered a Sikorsky HSS-1F in the U.S.'s first turbine-powered helicopter flight. That engine, which first ran in the 1950s, was the precursor of Lynn's small engine product line.
The 1950s and 1960s saw further advances. The J93 was developed to power the world’s largest, highest flying, and fastest bomber, the US Air Force’s experimental XB-70 Valkyrie. Six 28,800 lb thrust turbojets propelled the 500,000 lb demonstrator to three times the speed sound at an altitude of 74,000 feet. Technologies pioneered in the J93 are used in today’s military and commercial engines.
A major success of the period was the Lynn-manufactured J85 turbojet engine. Contracted by the USAF to build a low-cost air-combat fighter, Northrop built the F-5 Freedom Fighter around the GE J85 engine. The F-5 soon became the standard air defense aircraft for more than 30 nations. The J85 powers the US Air Force T-38 Talon supersonic pilot trainer.
GE introduced the T64 free-turbine turboshaft/turboprop engine in 1964, featuring technical innovations such as corrosion resistant and high-temperature coatings that contributed to the development of very heavy lift helicopters. The T64 was used on the Sikorsky CH-53 Sea Stallion family of helicopters that serve the US Navy, U.S. Marine Corps and several international militaries.
When the U.S. Navy needed a durable and efficient engine to power the Lockheed S-3 Viking for carrier based anti-submarine warfare, GE responded with the TF34 high bypass engine. The TF34 was also selected by the U.S. Air Force to power the A-10 Thunderbolt II close air support aircraft.
Advances in compressor, combustor and turbine knowledge in the 1960s led to the decision to propose a more compact core engine with a single-stage turbine and only two bearing areas versus three, resulting in the GE F101 engine, selected for the U.S. Air Force's B-1 bomber.
In the early 1970s, the Army turned to GE for an improved turboshaft engine to power its new generation of helicopters. The result was the legendary T700. Capitalizing on the lessons of the Vietnam War, the T700 provided the Army exceptionally reliable power built using a revolutionary modular architecture. The modular T700 was designed for field maintainability to drive down costs and improve Army helicopter readiness rates. Over the ensuing decades, multiple advanced technology upgrades were introduced for the T700. Also, the T700-derived, CT7 turboshaft and turboprop engine family was introduced for the commercial market. More than 25,000 T700/CT7 engines have been delivered. Since their introduction more than 40 years ago, the T700 and CT7 variants continue to establish new applications as one of the among popular turboshaft and turboprop engine families in aviation history.
The role of GE military engines continued to grow during the defense buildup of the 1980s. In 1984, the USAF selected GE's highly reliable F110 engine, based on the F101 design, for the F-16C/D fighter aircraft, initiating "The Great Engine War"- an intense, competition between GE and rival Pratt & Whitney. The F110 now powers the majority of USAF F-16C/Ds. The F110 also powers F-16s worldwide, having been selected by Israel, Greece, Turkey, Egypt, Bahrain, United Arab Emirates, Chile and Oman. In addition, the F110 powers Japan's single-engine F-2 fighter and the export versions of the F-15 Eagle operated by Korea, Saudi Arabia and Singapore. From the late 1980s through 2006, the US Navy operated an upgraded version of the F-14 Tomcat with the F110 engine. A derivative of the F110, the F118, powers the U.S. Air Force B-2 stealth bomber and U-2S high altitude reconnaissance aircraft.
Also in the 1980s, the F404 engine for the F/A-18 Hornet entered production. The F404 is the world's most ubiquitous fighter engine, with more than 3,700 powering 10 aircraft types worldwide. These include the Boeing F/A-18 Hornet, Saab JAS 39 Gripen, Korea’s T-50, India’s Tejas Mark I and the Lockheed Martin F-117 stealth fighter prior to its retirement in 2008.
GE is positioned to be a world leader in military propulsion well into the 21st century. The F414, the turbofan engine for the F/A-18E/F Super Hornet front-line strike fighter and EA-18G Growler electronic attack aircraft, produces 22,000 pounds of thrust. It is also the engine of choice for the JAS 39E Gripen Next Generation and HAL Tejas Mark II. GE Aerospace has the capability to increase F414 durability and thrust by as much as 25 percent.
GE first received funding to begin developing a competitive engine for the Joint Strike Fighter (JSF) in 1996 and ultimately teamed with Rolls Royce for the full-scale development contract. The team successfully completed Short Take Off, Vertical Landing (STOVL) testing on an F136 engine at the GE testing facility at Peebles, Ohio in 2008. Extensive ground testing of the F136, designed for all variants of the JSF aircraft for the Air Force, Navy and Marine Corps, included the first use of ceramic matric composites in GE-designed components and paved the way for expanded use of these revolutionary materials in GE’s next generation commercial engines and military engines.
Due to US Government fiscal challenges and DoD budget cuts, Congress made the decision in 2011 to discontinue funding development of the F136 and the program was cancelled after about 80% completion.
Building on the strength of its design capabilities for high performance combat aircraft engines, GE successfully completed testing the world’s first adaptive, three-stream engine in 2014 through the Adaptive Versatile Engine Technology (ADVENT) program with the United States Air Force Research Lab.
By the next decade, the adaptive cycle (also called variable cycle) engine could revolutionize jet fighters. The variable cycle engine alternatives between a high-thrust mode for maximum power and a high-efficiency mode for optimum fuel savings and greater aircraft range. In 2018, the USAF awarded to GE a $437 million contract to further advance adaptive-cycle engine technology, bolstering the company’s 11-year effort in this technology dating back to 2007.
GE’s next-generation military portfolio also includes the T901 turboshaft (downselected by the U.S. government in 2019) now under development, and also, the T408 turboshaft for heavy lift missions of the new Sikorsky CH-53 King Stallion for the U.S. Marine Corps. Capable of producing more than 7,500 shaft horsepower, the T408 combines breakthrough technologies, innovative cooling schemes and durability to deliver numerous mission-critical advantages in the world’s harshest operating environments.
The T901 is being designed as a replacement for the T700 engine powering existing Black Hawk and Apache helicopters through the U.S. Army’s Improved Turbine Engine Program (ITEP). Compared to the most advanced T700 engines in service, the T901 provides 25 percent better fuel economy, 35 percent lower acquisition and maintenance costs, 20 percent longer life and as much as 65 percent more power to weight.
GE Aerospace invests more than $1 billion each year in research and development, positioning the company to lead advancements in military propulsion for generations to come.
Add Attachment

Share
Recent Chats
Share via email
Future: handle WhatsApp here
Future: handle LinkedIn here
Future: handle Twitter here
SUBMENU HERE
Share via Chat
Copy Link