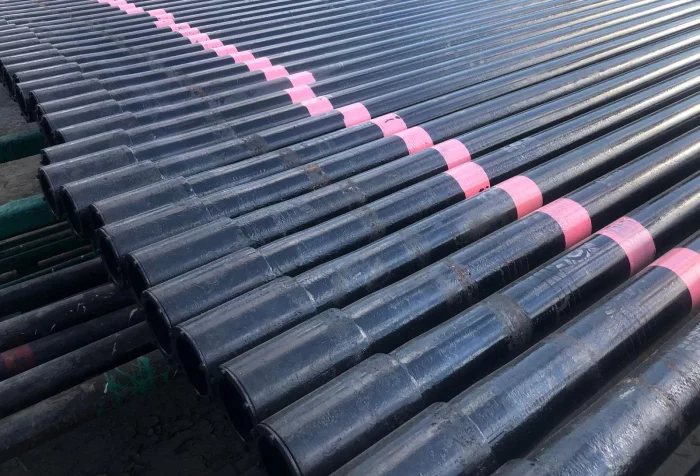
_300.webp)
BLUEWATER THERMAL SOLUTIONS
Houston, Texas (TX), United States
Oil · Gas · Energy
Products & Services
People
About
About
Bluewater Thermal Solutions produces BOR-1Cr Boronized OCTG tubing that is used in oil wells to prevent hole in tubing failures and extend the run time of each well.
Boronizing is a diffusion case hardening process where boron is diffused into the surface of steel tubing where it reacts with iron to form a hard, corrosion resistant subsurface layer of iron-boride compounds (FeB and Fe2B) This iron-boride layer has a hardness of 1500 Vickers and can withstand rod wear and sand erosion to prevent holes in tubing as the iron boride layer is 20x more wear resistant than untreated tubing. The boronized surfaces are also 6x more corrosion resistant in the downhole environment that consists of H2S, CO2, brine water, high temperature and high pressure as compared to 13Cr tubing. This combination of ultra-high wear and erosion resistance combined with excellent corrosion resistance makes BOR-1Cr tubing last much longer than standard tubing which reduces expensive workover frequencies, costly downtime and loss of production.
Boronized steel is also not a coating where the iron-boride layer cannot come loose or break off of the tubing surface since it is diffused into the steel.
Boronized tubing has been accepted for widespread use across the United States with many major producers including Conoco Phillips, Hess Oil, Marathon Oil, Oxy, Pioneer Natural Resources, XTO Energy and many other operators. Boronizing is also used on many other components such as plungers, sand separators, desanding mandrels, gas lift mandrels, and rod couplings where each of those components can fail prematurely due to wear, sand erosion or corrosion.
Boronizing is a diffusion case hardening process where boron is diffused into the surface of steel tubing where it reacts with iron to form a hard, corrosion resistant subsurface layer of iron-boride compounds (FeB and Fe2B) This iron-boride layer has a hardness of 1500 Vickers and can withstand rod wear and sand erosion to prevent holes in tubing as the iron boride layer is 20x more wear resistant than untreated tubing. The boronized surfaces are also 6x more corrosion resistant in the downhole environment that consists of H2S, CO2, brine water, high temperature and high pressure as compared to 13Cr tubing. This combination of ultra-high wear and erosion resistance combined with excellent corrosion resistance makes BOR-1Cr tubing last much longer than standard tubing which reduces expensive workover frequencies, costly downtime and loss of production.
Boronized steel is also not a coating where the iron-boride layer cannot come loose or break off of the tubing surface since it is diffused into the steel.
Boronized tubing has been accepted for widespread use across the United States with many major producers including Conoco Phillips, Hess Oil, Marathon Oil, Oxy, Pioneer Natural Resources, XTO Energy and many other operators. Boronizing is also used on many other components such as plungers, sand separators, desanding mandrels, gas lift mandrels, and rod couplings where each of those components can fail prematurely due to wear, sand erosion or corrosion.
Add Attachment

Share
Recent Chats
Share via email
Future: handle WhatsApp here
Future: handle LinkedIn here
Future: handle Twitter here
SUBMENU HERE
Share via Chat
Copy Link