_700.webp)
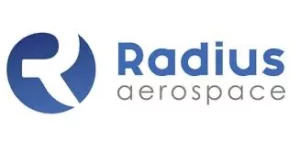
Super Plastic Forming / Hot Forming of Titanium
Heat shields, frames, hot section components
Exhaust Systems
Engine exhaust plug and nozzle, duct assemblies, APU exhausts
Leading Edges
Wing and empennage leading edge assemblies, stretch-formed skins
Engine Components and Assemblies
Combustion liners, rings, seals, blade vanes, fabricated assemblies
RADIUS AEROSPACE
See us at Farnborough International Airshow 2026 · Booth: 3131
Radius Aerospace is a leading provider of fabrications and assemblies to the premier aerospace OEMs across civil, military, and business jet markets as well as integrated assemblies for the industrial gas turbine market. Our four vertically integrated facilities in the United States and the UK produce highly complex assemblies for the aerostructure and propulsion segments. Core services include the forming, welding, bonding, shaping and assembly of specialty metallic structures, utilizing multiple special processes.
Hot Springs, Arkansas (AR), United States
Aerospace, Defense & Security
Products & Services
People
About
Connect with us at
Products & Services
Welding
Radius Aerospace
Complex assemblies in inconel, titanium, steel, aluminum and other specialty alloys
Automated Manufacturing
Radius Aerospace
Lights out manufacturing on multiple processes
Core Services
Radius Aerospace
In addition to these traditional aerospace manufacturing services, Radius provides enhanced capabilities including specialty alloy welding, titanium hot forming & super plastic forming (SPF), bulge forming, large stretch-forming of sheet and extrusion, complex mechanical assembly, chemical milling, titanium Sol-Gel and ti-foil, metal to metal and composite bonding, 5-axis CNC machining, trimming and drilling, high-speed laser and waterjet cutting, hydroforming, and electroforming. Augmenting these core competencies are additional process capabilities including clean lines, drop-bottom heat-treat, autoclaves and ovens, automated grinding and EDM cells, processing and paint. Close tolerance applications with the highest quality standards are inherent in everything we do.
Fire shields
Radius Aerospace
Fabricated weldments
Fluid Presses
Radius Aerospace
Extrusion press for longerons, stringer, frames and other formed details
Processing
Radius Aerospace
Processing in every facility
Assembly
Radius Aerospace
Airframe structures, exhaust systems, engine sub-assemblies and specialty land, marine and IGT applications
Hot Forming / Super Plastic Forming (SPF)
Radius Aerospace
Complex deep-draw close tolerance shapes up to 7 ft x 5 ft
Heat treatment
Radius Aerospace
Autoclaves for metallic and composite bonding, heat-treat, anneal, stress relief, hardening and age ovens.
Engine blades and vanes
Radius Aerospace
(2) New state-of-the-art, automated, palletized M7 grinding cell with EDM, CMM and Kuka Robots.
Engine Components
Radius Aerospace
Combustion liners, rings, seals, and much more
Exhaust systems
Radius Aerospace
Bulge-formed, welded chem-milled, inconel plugs, nozzels, and complete exhaust systems
EB Welding
Radius Aerospace
1.3m envelop
Product Portfolio
Radius Aerospace
Radius provides structural components and assemblies on aircraft, rotorcraft, hypersonic systems, land and marine systems, industrial gas turbine and adjacent platforms. Core product lines include exhaust systems, combustion liners, wing leading edges, fuselage panels, fire shields, metal to metal and metal to composite bonded panels, and much more.
Model-based full-size hole capability
Radius Aerospace
Temperature controlled environments, specialized forming processes
Automated Grinding and EDM Cells
Radius Aerospace
Precision single-piece Kuka robot automated processes including grinding, electronic deposition machining (EDM) and CMM stations, primarily used for aircraft and industrial gas turbine engine blades and blade vanes.
Hydro-bulge forming
Radius Aerospace
Up to 4 ft diameter, 6 ft deep
Non-conventional machining
Radius Aerospace
Minimal heat-affected zones eliminating recast
Leading Edge Assemblies
Radius Aerospace
Commercial, Military and Biz-Jet applications
Fabricated Assemblies
Radius Aerospace
Aluminum, steel and titanium fabrications
CNC Machining
Radius Aerospace
Aluminum, steel, titanium and specialty metals
Hot-Formed and Super Plastic Formed (SPF) titanium
Radius Aerospace
Deep draw, close tolerance formed titanium sheet applications
Chemical Milling
Radius Aerospace
For use on fuselage skins, leading edges, and multiple nacelle applications
People
Connect with us at
About
In addition to these traditional aerospace manufacturing services, Radius provides enhanced capabilities including specialty alloy welding, titanium hot forming & super plastic forming (SPF), bulge forming, large stretch-forming of sheet and extrusion, complex mechanical assembly, chemical milling, titanium Sol-Gel and ti-foil, metal to metal and composite bonding, 5-axis CNC machining, trimming and drilling, high-speed laser and waterjet cutting, hydroforming, and electroforming. Augmenting these core competencies are additional process capabilities including clean lines, drop-bottom heat-treat, autoclaves and ovens, automated grinding and EDM cells, processing and paint. Close tolerance applications with the highest quality standards are inherent in everything we do.
Radius provides structural components and assemblies on aircraft, rotorcraft, hypersonic systems, land and marine systems, industrial gas turbine and adjacent platforms. Core product lines include exhaust systems, combustion liners, wing leading edges, fuselage panels, fire shields, metal to metal and metal to composite bonded panels, and much more. Radius employs more than 900 dedicated team members across nearly 1 million square feet of manufacturing space. We currently have fully operational facilities in Hot Springs, Arkansas; Phoenix, Arizona; Shelbyville, Indiana; and Sheffield, UK.
Radius provides structural components and assemblies on aircraft, rotorcraft, hypersonic systems, land and marine systems, industrial gas turbine and adjacent platforms. Core product lines include exhaust systems, combustion liners, wing leading edges, fuselage panels, fire shields, metal to metal and metal to composite bonded panels, and much more. Radius employs more than 900 dedicated team members across nearly 1 million square feet of manufacturing space. We currently have fully operational facilities in Hot Springs, Arkansas; Phoenix, Arizona; Shelbyville, Indiana; and Sheffield, UK.
Add Attachment

Share
Recent Chats
Share via email
Future: handle WhatsApp here
Future: handle LinkedIn here
Future: handle Twitter here
SUBMENU HERE
Share via Chat
Copy Link