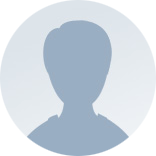
Jeff Prom
President
Jeff Prom')>
About
Cutting Tools that can cut anything. Even time.
Cut costs, save money—it’s the continual battle. So you look for less expensive tooling options, which may or may not be the answer in the long run. But what if the solution wasn’t a cheaper tool, but rather a better process? That’s the first step in the Sharon-Cutwell® approach. Over the past 70 years, we’ve seen virtually every conceivable tooling application. And rather than simply providing the tool you think you want, we’ll suggest process changes to help you reduce your manufacturing cycle times and deliver greater throughput. Then we’ll design the best tool for that process. You may call it a tool. We call them time machines.
What do you need your cutting tool to do?
That should be the first question your cutting tool supplier asks you. Today, designing and manufacturing cutting tools for metalworking, woodworking and specialized composite materials is becoming increasingly complex. Challenging materials, intricate geometries, multiple component sizes and specialized needs require a partner with the engineering talent and equipment to solve difficult projects. Our cutting tools solve unique manufacturing problems by transferring complexity from the job to the tool. If we know what you want to do or the problems you seek to avoid, we can design a solution that meet all critical criteria. The result is precise and consistent cutting tool performance with exceptional tool life. All of which ultimately saves time and money.
Sharon-Cutwell® is heavily invested in the newest CNC technology, precision measuring devices and 3-D design software. More important, our associates possess the knowledge, skill and dedication to craft unique cutting tools to exacting specifications. With an average employee tenure of more than 12 years, you can trust the quality and performance of Cutwell metalworking and composite cutting tools.
Cut costs, save money—it’s the continual battle. So you look for less expensive tooling options, which may or may not be the answer in the long run. But what if the solution wasn’t a cheaper tool, but rather a better process? That’s the first step in the Sharon-Cutwell® approach. Over the past 70 years, we’ve seen virtually every conceivable tooling application. And rather than simply providing the tool you think you want, we’ll suggest process changes to help you reduce your manufacturing cycle times and deliver greater throughput. Then we’ll design the best tool for that process. You may call it a tool. We call them time machines.
What do you need your cutting tool to do?
That should be the first question your cutting tool supplier asks you. Today, designing and manufacturing cutting tools for metalworking, woodworking and specialized composite materials is becoming increasingly complex. Challenging materials, intricate geometries, multiple component sizes and specialized needs require a partner with the engineering talent and equipment to solve difficult projects. Our cutting tools solve unique manufacturing problems by transferring complexity from the job to the tool. If we know what you want to do or the problems you seek to avoid, we can design a solution that meet all critical criteria. The result is precise and consistent cutting tool performance with exceptional tool life. All of which ultimately saves time and money.
Sharon-Cutwell® is heavily invested in the newest CNC technology, precision measuring devices and 3-D design software. More important, our associates possess the knowledge, skill and dedication to craft unique cutting tools to exacting specifications. With an average employee tenure of more than 12 years, you can trust the quality and performance of Cutwell metalworking and composite cutting tools.

Share
Recent Chats
Share via email
Future: handle WhatsApp here
Future: handle LinkedIn here
Future: handle Twitter here
SUBMENU HERE
Share via Chat
Copy Link