Software Development
TURBOCAM got its start by developing unique 5-axis algorithms for more precise machine motion. Those very first ideas and that initial software set us apart and gave us a deeper understanding of CAD geometry and CAM generated toolpaths.
Description
More Products & Services
Products & Services
Engineering Solutions
TURBOCAM International
The stages of cost reduction and design for manufacturing are critical steps in becoming competitive for market. Expertise in this has made TURBOCAM the supplier of choice for bladed production parts for many of the world’s leading manufacturers of turbomachinery and aero engines.
TURBOCAM engineers offer their skills in:
Geometric modeling and analysis
Aerodynamics
Metallurgy and metal chemistry
Measurement systems
Statistical quality control and analysis
TURBOCAM wants designers to get what they need for aerodynamic efficiency and structural integrity, rather than compromise to save cost. By working with TURBOCAM, clients can get the best combinations in arbitrary surface designs and root structures without breaking the bank.
The company’s command of surface modeling and machining practice can zero in on excellent flow paths and structures. Plenty of pitfalls remain in material selection and vendor processes. The skills and experience at TURBOCAM can abate them.
For higher temperature applications, where nickel alloys are used, the combination of 5-axis milling and electrochemical dissolution offers rare and unique solutions to gain fatigue resistance along with desired geometric shape.
TURBOCAM engineers offer their skills in:
Geometric modeling and analysis
Aerodynamics
Metallurgy and metal chemistry
Measurement systems
Statistical quality control and analysis
TURBOCAM wants designers to get what they need for aerodynamic efficiency and structural integrity, rather than compromise to save cost. By working with TURBOCAM, clients can get the best combinations in arbitrary surface designs and root structures without breaking the bank.
The company’s command of surface modeling and machining practice can zero in on excellent flow paths and structures. Plenty of pitfalls remain in material selection and vendor processes. The skills and experience at TURBOCAM can abate them.
For higher temperature applications, where nickel alloys are used, the combination of 5-axis milling and electrochemical dissolution offers rare and unique solutions to gain fatigue resistance along with desired geometric shape.
Integrated Product Development
TURBOCAM International
Getting a product to market includes solving engineering problems (like vibration), sources of error (like assembly), and material sourcing (from near and far). Added to the machining is manufacturing optimization for reduced HCF and LCF effects, metallurgy improvement by diffusion (in steels), process engineering, statistical quality analysis and reporting, NDT, coatings, and allied services by subcontractors.
Quality Assurance
TURBOCAM International
TURBOCAM’s headquarters division and aerospace production unit share certification to the AS9100 standard in all areas except design. Whether we meet the varied and demanding requirements of our customers is verified by a variety of tactile and laser scanning CMMs, precision gaging, and on-machine measurement capabilities. An in-house NDT department provides NAS 410 compliant fluorescent penetrant inspection (FPI). Real-time SPC is utilized on the higher volume production programs for improved process control.
The TURBOCAM Automated Production Systems (TAPS) is a high-volume producer of turbocharger components, certified to the IATF16949 standard, excluding design. Product inspection utilizing DCC-CMMs and precision gaging is integrated into the production process along with real-time SPC. These tools provide the foundation to improve quality and ensure effective process control, leading to smarter business decisions. Delivering in excess of 1 million components each year, the quality of materials provided by the supply chain is actively managed through our Supplier Quality program, assuring uninterrupted component supply lines.
TURBOCAM’s Automated Production System in Charleston, South Carolina features a turbocharger component assembly operation certified to the IATF 16949 and ISO 9001:2015 standards, excluding design. Its quality system is integrated with the TAPS business unit, including production SPC monitoring and quality management system software.
The TURBOCAM Automated Production Systems (TAPS) is a high-volume producer of turbocharger components, certified to the IATF16949 standard, excluding design. Product inspection utilizing DCC-CMMs and precision gaging is integrated into the production process along with real-time SPC. These tools provide the foundation to improve quality and ensure effective process control, leading to smarter business decisions. Delivering in excess of 1 million components each year, the quality of materials provided by the supply chain is actively managed through our Supplier Quality program, assuring uninterrupted component supply lines.
TURBOCAM’s Automated Production System in Charleston, South Carolina features a turbocharger component assembly operation certified to the IATF 16949 and ISO 9001:2015 standards, excluding design. Its quality system is integrated with the TAPS business unit, including production SPC monitoring and quality management system software.
High Volume Production
TURBOCAM International
Since 2001: We automated the manufacturing of machined-from-solid (MFS) aluminum and titanium compressor impellers, with the goal of running 24/7 and unmanned on Sundays.
Since 2014: We have manufactured thousands of compressor vanes for aircraft engines using Electrochemical machining.
The TURBOCAM plants in Barrington have numerous robots and machine tools that produce compressor impellers and vanes and monitor the process continuously to assure that quality is never compromised. Close tolerances and surface finishes required for high performance turbomachinery applications are statistically measured and analyzed.
These plants are supported by TURBOCAM plants in England, Romania and India, with similar technology and growing levels of automation and infrastructure.
This manufacturing technology initially applied to automotive turbochargers is also applicable for micro turbines, turbojet engines, air cycle machines, and air conditioners.
Since 2014: We have manufactured thousands of compressor vanes for aircraft engines using Electrochemical machining.
The TURBOCAM plants in Barrington have numerous robots and machine tools that produce compressor impellers and vanes and monitor the process continuously to assure that quality is never compromised. Close tolerances and surface finishes required for high performance turbomachinery applications are statistically measured and analyzed.
These plants are supported by TURBOCAM plants in England, Romania and India, with similar technology and growing levels of automation and infrastructure.
This manufacturing technology initially applied to automotive turbochargers is also applicable for micro turbines, turbojet engines, air cycle machines, and air conditioners.
Prototyping
TURBOCAM International
Our teams of engineers and machinists at facilities in America, Europe, and Asia process 500-1000 unique prototype designs every year, some for test, some for early market penetration, and some destined to be made in the thousands or millions. We support the latest innovations and advanced part development for jet aircraft engines, rocket engines, turbochargers for truck engines, power generation, and petrochemical applications. This includes diameters from 10mm to 1100mm, and very basic airfoil shapes as well as advanced integrally shrouded designs. TURBOCAM can adapt to address your unique prototyping needs.
Metallurgical Solutions
TURBOCAM International
Our approach to metallurgy
TURBOCAM uses our metallurgical knowledge to provide elegant solutions with selected materials, saving our customers from overbuilt designs or high-cost alloys. We also improve the characteristics of lower-cost materials through surface diffusion and finishing methods, enabling our parts to outperform more expensive materials.
Our unique thermal diffusion surface transformation technologies can improve the wear resistance of some steels without increasing bulk hardness and creating brittleness. While our claim to fame is in wear resistance at high temperatures, we have seen great improvements in resistance to crack propagation.
TURBOCAM uses our metallurgical knowledge to provide elegant solutions with selected materials, saving our customers from overbuilt designs or high-cost alloys. We also improve the characteristics of lower-cost materials through surface diffusion and finishing methods, enabling our parts to outperform more expensive materials.
Our unique thermal diffusion surface transformation technologies can improve the wear resistance of some steels without increasing bulk hardness and creating brittleness. While our claim to fame is in wear resistance at high temperatures, we have seen great improvements in resistance to crack propagation.
Abradable Coatings
TURBOCAM International
Sustainable jet engines start with the right materials and coatings, which is why our customers use our abradable plasma coating. These coatings serve as a sacrificial layer to eliminate damage to expensive base materials. Abradable coatings also allow for a better seal between mating surfaces, which can boost engine efficiency.
We provide our customers high quality coatings with our combination of robotic programming, IMR-trained lab staff, and plasma spray technicians. Our expertise has led to TES achieving NADCAP Merit Status, an award that recognizes excellence in quality and engineering of aerospace coatings. Our certifications below reflect our team’s dedication to quality results.
We provide our customers high quality coatings with our combination of robotic programming, IMR-trained lab staff, and plasma spray technicians. Our expertise has led to TES achieving NADCAP Merit Status, an award that recognizes excellence in quality and engineering of aerospace coatings. Our certifications below reflect our team’s dedication to quality results.
Electrochemical Machining
TURBOCAM International
ECM is a complex and powerful manufacturing technique which can create features without the typical constraints of mechanical cutting and forming, since it has a lower concentration of heat and force, relying on electrical and chemical potential instead. TURBOCAM primarily uses several pulsed energy techniques which are commonly called “PECM” and achieve exceptionally high precision.
People
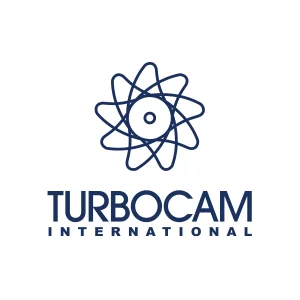
Jenn Broadbent
TURBOCAM International
Director Admin & Communications Support
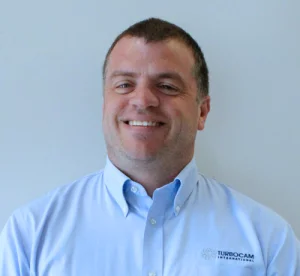
Jim Cooper
TURBOCAM International
General Manager, TURBOCAM AeroEngines
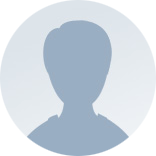
Jim Quinney
TURBOCAM International
General Manager
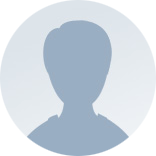
Levlin Colaco
TURBOCAM International
Project Manager
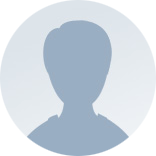
Marian Noronha
TURBOCAM International
President
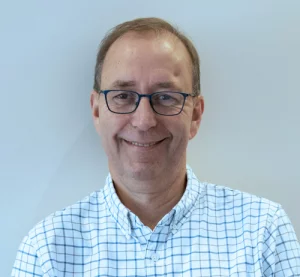
Onno Weststrate
TURBOCAM International
Business Development Manager
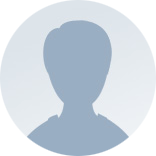
Tim Noronha
TURBOCAM International
General Manager
Description
Our legacy still drives us today. A deep understanding of CAD geometry and CAM generated toolpaths is one of the keys to TURBOCAM’s success in manufacturing complex turbomachinery components.
Our in-house CAD/CAM development provides us with:
• Customized toolpath strategies for turbomachinery parts
• Customized visualization and feedback tailored to our engineering processes
• Precise control over toolpath inputs and outputs
• Ability to create unique solutions to specific manufacturing challenges
TURBOCAM makes thousands of parts every day, and each part goes through a variety of manufacturing and inspection operations before it is complete. A lot of data is generated from all of these operations. We develop custom software solutions, where needed, to meet the challenge of keeping it all organized.
Our quality and operations solutions help us:
• Capture and understand data generated from our manufacturing processes
• Automate part pathways based on inspection results
• Customize feedback to the shop floor and management
• Quickly meet changing requirements of our manufacturing processes
• Freely create specialized solutions
Our in-house CAD/CAM development provides us with:
• Customized toolpath strategies for turbomachinery parts
• Customized visualization and feedback tailored to our engineering processes
• Precise control over toolpath inputs and outputs
• Ability to create unique solutions to specific manufacturing challenges
TURBOCAM makes thousands of parts every day, and each part goes through a variety of manufacturing and inspection operations before it is complete. A lot of data is generated from all of these operations. We develop custom software solutions, where needed, to meet the challenge of keeping it all organized.
Our quality and operations solutions help us:
• Capture and understand data generated from our manufacturing processes
• Automate part pathways based on inspection results
• Customize feedback to the shop floor and management
• Quickly meet changing requirements of our manufacturing processes
• Freely create specialized solutions

Share
Recent Chats
Share via email
Future: handle WhatsApp here
Future: handle LinkedIn here
Future: handle Twitter here
SUBMENU HERE
Share via Chat
Copy Link