SkoFlo pressure independent chemical injection metering valves allow one pump to be shared by several injection points, thereby reducing facility costs and maintenance costs. As an added benefit, SkoFlo valves are maintenance-free; while pumps may require several seal changes over the life of the project.
Description
More Products & Services
Products & Services
Subsea Back Pressure Regulator (BPR)
SkoFlo Industries Inc
SkoFlo Subsea Back Pressure Regulators (BPRs) are anti-siphoning devices that create back pressure in chemical injection lines to prevent uncontrolled delivery of chemicals into production wells caused by fluid siphoning.
Subsea BPRs regulate inlet pressure when the well pressure falls below the factory set point of the device.
The Subsea BPR is a self-regulating device activated only when required
Two Stage Device: Cavitation is reduced or eliminated by separating the pressure drop across two stages.
Utilizing two stages allows for larger fluid paths, resulting in a higher debris tolerance, longer device life, and lower design and operating pressures of topside chemical injection systems.
Subsea BPRs can be installed on subsea trees, manifolds, logic caps, and Multi Quick Connect (MQC) plates.
Subsea BPRs regulate inlet pressure when the well pressure falls below the factory set point of the device.
The Subsea BPR is a self-regulating device activated only when required
Two Stage Device: Cavitation is reduced or eliminated by separating the pressure drop across two stages.
Utilizing two stages allows for larger fluid paths, resulting in a higher debris tolerance, longer device life, and lower design and operating pressures of topside chemical injection systems.
Subsea BPRs can be installed on subsea trees, manifolds, logic caps, and Multi Quick Connect (MQC) plates.
Surface Back Pressure Regulator (BPR)
SkoFlo Industries Inc
Back Pressure Regulator (BPR) maintains constant set pressure in pump discharge lines feeding the chemical injection system while recycling unused fluid to the chemical holding tank.
Provide constant and stable pressure to the system over a wide range of flow with continuous spill-off to the chemical tank.
Robust design with ceramic trim will handle the full pressure drop throughout the entire flow range
Reliable and accurate pressure regulation for the life of the system
No scheduled maintenance
Low torque handle
Pressure Rating up to 15,000 psi with Flow ranges as low as 2 GPD and as high as 15 GPM
Provide constant and stable pressure to the system over a wide range of flow with continuous spill-off to the chemical tank.
Robust design with ceramic trim will handle the full pressure drop throughout the entire flow range
Reliable and accurate pressure regulation for the life of the system
No scheduled maintenance
Low torque handle
Pressure Rating up to 15,000 psi with Flow ranges as low as 2 GPD and as high as 15 GPM
Surface Integrated Topside Actuator, Valve and PDFM (SF3)
SkoFlo Industries Inc
Fully automated chemical injection metering package combining measurement, actuation and control using an integrated Positive Displacement Flow Meter (PDFM), Actuator, and Chemical Injection Metering Valve (CIMV)
Chemical Injection Metering Valve (CIMV) incorporates the same pressure independent SkoFlo design that is field proven and tested in the harshest environments for over 30 years with over 20,000 valves in service.
Positive Displacement Flow Meter (PDFM) developed by SkoFlo and deployed in subsea CIMVs since 2011 offers true volumetric flow measurement for reliable and accurate flow measurement down to 0.6 gallons per day.
Smaller footprint architecture provides several important benefits:
Reduced cost
Reduced weight
Easily reconfigurable
Minimal intervention, easy to install and maintain
Reduces Platform Maintenance by eliminating system leak points from typical tubing and fittings
High turndown ratio
ATEX, IECEx, ETL Certified
Optional downstream pressure sensor available for improved performance, diagnostics, and cost savings
Highly accurate flow measurement of ±0.5% of reading.
Continuous Setpoint Regulation (CSR) – SF3 automatically adjusts set point if needed to maintain consistent and accurate chemical injection in the event of extreme temperature variations.
Autonomous Flow Measurement (AFM) – SF3 can be programmed to take periodic flow readings as needed.
Zero Flow Shutdown (ZFS) – If flow stops the valve will be shutdown to prevent excess pumping of fluids when the pumps come back on.
Chemical Injection Metering Valve (CIMV) incorporates the same pressure independent SkoFlo design that is field proven and tested in the harshest environments for over 30 years with over 20,000 valves in service.
Positive Displacement Flow Meter (PDFM) developed by SkoFlo and deployed in subsea CIMVs since 2011 offers true volumetric flow measurement for reliable and accurate flow measurement down to 0.6 gallons per day.
Smaller footprint architecture provides several important benefits:
Reduced cost
Reduced weight
Easily reconfigurable
Minimal intervention, easy to install and maintain
Reduces Platform Maintenance by eliminating system leak points from typical tubing and fittings
High turndown ratio
ATEX, IECEx, ETL Certified
Optional downstream pressure sensor available for improved performance, diagnostics, and cost savings
Highly accurate flow measurement of ±0.5% of reading.
Continuous Setpoint Regulation (CSR) – SF3 automatically adjusts set point if needed to maintain consistent and accurate chemical injection in the event of extreme temperature variations.
Autonomous Flow Measurement (AFM) – SF3 can be programmed to take periodic flow readings as needed.
Zero Flow Shutdown (ZFS) – If flow stops the valve will be shutdown to prevent excess pumping of fluids when the pumps come back on.
Subsea Chemical Injection Metering Valves (CIMV)
SkoFlo Industries Inc
Pressure-balanced piston: Pressure independence, which is unique to SkoFlo Chemical Injection Metering Valves,
constantly delivers accurate and precise chemical injection.
SkoFlo’s Chemical Injection Metering Valve (CIMV) maintains set chemical injection flow rates regardless of upstream (platform to the valve) and downstream (valve to the well) pressure fluctuations. Upstream and downstream pressure fluctuations create a net force on the piston, which is countered by a spring force to maintain constant flow.
SkoFlo’s innovative pressure-balanced piston design allows chemicals to be distributed at different injection points from a common line. This reduces the number of umbilicals, and in turn, significantly reduces the cost to the operator. The spring balanced piston also provides a means of control that is more tolerant to debris and fluid filming than a throttling stem directly driven by a gear motor.
Large particle debris produce a net force on the piston; pressure created on the piston surfaces by debris is pushed out through the outlet instantaneously. Response time occurs within milliseconds with no “hunting” or control iterations as opposed to a motor operated stem that needs to open and close, also known as dithering.
Fail “as-is without drift” – During loss of power the valve will continue to regulate flow at the set flow rate, regardless of debris or system pressure fluctuations.
The SkoFlo Positive Displacement Flow Meter (PDFM) provides accurate flow measurements of better than ±2% of
reading and measures flow rates down to 1 GPD and as high as 97 GPM
constantly delivers accurate and precise chemical injection.
SkoFlo’s Chemical Injection Metering Valve (CIMV) maintains set chemical injection flow rates regardless of upstream (platform to the valve) and downstream (valve to the well) pressure fluctuations. Upstream and downstream pressure fluctuations create a net force on the piston, which is countered by a spring force to maintain constant flow.
SkoFlo’s innovative pressure-balanced piston design allows chemicals to be distributed at different injection points from a common line. This reduces the number of umbilicals, and in turn, significantly reduces the cost to the operator. The spring balanced piston also provides a means of control that is more tolerant to debris and fluid filming than a throttling stem directly driven by a gear motor.
Large particle debris produce a net force on the piston; pressure created on the piston surfaces by debris is pushed out through the outlet instantaneously. Response time occurs within milliseconds with no “hunting” or control iterations as opposed to a motor operated stem that needs to open and close, also known as dithering.
Fail “as-is without drift” – During loss of power the valve will continue to regulate flow at the set flow rate, regardless of debris or system pressure fluctuations.
The SkoFlo Positive Displacement Flow Meter (PDFM) provides accurate flow measurements of better than ±2% of
reading and measures flow rates down to 1 GPD and as high as 97 GPM
People
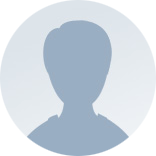
Amanda Crabtree
SkoFlo Industries Inc
Executive Assistant & Sales Administrator
ADIPEC 2025
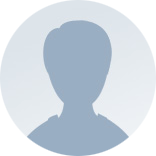
Justin Calkins
SkoFlo Industries Inc
SF3 Product Manager
ADIPEC 2025
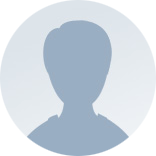
Mike Pachul
SkoFlo Industries Inc
Business Development Director (Eastern Hemisphere)
ADIPEC 2025
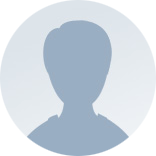
Sales Team
SkoFlo Industries Inc
Sales Team
ADIPEC 2025
Description
Pressure Rating up to 15,000 psi
Flow ranges as low as 0.2 GPD and as high as 40 GPM
PRESSURE INDEPENDENT
Upstream and downstream pressure fluctuations create a net force on the patented pressure balanced piston, which is countered by a spring force to maintain constant flow.
ACCURATE FLOW DELIVERY
Pressure‐balanced piston provides instantaneous means of control at different injection points from a common line that is more tolerant to debris and fluid filming. No pneumatic or electric power sources required for control.
Flow ranges as low as 0.2 GPD and as high as 40 GPM
PRESSURE INDEPENDENT
Upstream and downstream pressure fluctuations create a net force on the patented pressure balanced piston, which is countered by a spring force to maintain constant flow.
ACCURATE FLOW DELIVERY
Pressure‐balanced piston provides instantaneous means of control at different injection points from a common line that is more tolerant to debris and fluid filming. No pneumatic or electric power sources required for control.

Share
Recent Chats
Share via email
Future: handle WhatsApp here
Future: handle LinkedIn here
Future: handle Twitter here
SUBMENU HERE
Share via Chat
Copy Link