GE To Launch Emerging MRO Technologies At New Acceleration Center
Details
More Products & Services
Products & Services
Home - Aviation Group Marketing
Aviation Week Network
120 data points on over 156,000 commercial and business aviation aircraft, including military transports. Discover the most trustworthy resource for the complete aircraft history, plus ad hoc reports, month-over-month trend analysis and details on expected deliveries through 2050.
Aerospace | Aviation Week Network
Aviation Week Network
https://aviationweek.com/themes/custom/particle/dist/app-drupal/assets/awn-logo.svg
People
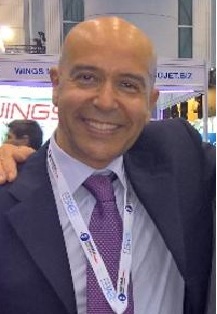
Andrea Rossi Prudente
Aviation Week Network
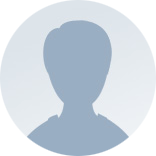
Becca Balmes
Aviation Week Network
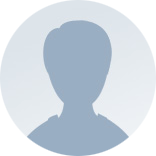
Belinda Tan
Aviation Week Network
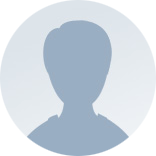
Brian Everstine
Aviation Week Network
Editor
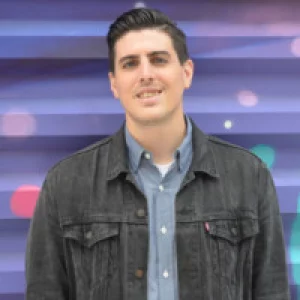
Eddie Krankowski
Aviation Week Network
Assistant Manager, Tradeshows
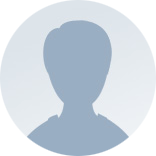
erving dockery
Aviation Week Network
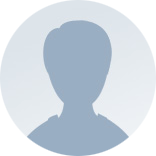
Lisa Tan
Aviation Week Network
Senior Marketing Manager
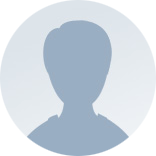
Mark Thomas
Aviation Week Network
Description
GE Aerospace will soon open the doors on its new Services Technology Acceleration Center, and the facility will be the launching ground for several new advanced inspection technologies aimed at simplifying MRO processes.
Set to open this month near GE's Cincinnati headquarters, the Services Technology Acceleration Center (STAC) will focus on advanced engine inspection, repair and overhaul technologies that the OEM wants to roll out across its global MRO network. According to Nicole Jenkins, chief MRO engineer at GE Aerospace, the facility “will serve as a major accelerator for scaling and deploying cutting edge inspection and repair processes to market.”
One of these technologies will be artificial intelligence (AI) guided white light robot inspections, which aim to ease physical strain on GE's technicians while providing consistency and efficiency benefits. Sam Blazek, services technology leader for white light inspection at GE Aerospace, says he previously had to conduct these types of inspections “caveman style” by hand with a flashlight and mirror, needing to move his head, eyes and neck to manipulate these tools and interpret what he was seeing. “Staring at the same part or feature for 8-12 hr. a day can make your head hurt,” he says.
The new inspection technology uses two articulated industrial robots outfitted with white light optical scanners to carefully move across the surface of a high-precision part, such as a turbine disk. Instead of requiring a human to visually interpret defects such as nicks, dents, scratches and corrosion, the system uses AI to capture and analyze data while creating a digital record of the part's condition. Although the technology automates the inspection itself, technicians will still examine the results on a screen to make a final call about inspection findings and serviceability.
“By using AI and robotics, service engineers can increase the speed and efficiency of part inspections while improving the consistency of their results,” says Jon Hootman, engineering director of the STAC. He adds that the technology is the first time GE has been able to completely digitally capture all characteristics of a part in service and catalog the data throughout its lifetime in a central repository.
“The beauty is that all of this together now pulls in the entire value stream to eradicate inconsistencies in your interpretation,” says Hootman. “[It allows us] to make sure that we are applying the appropriate level of consistency and interpretation to the anomalies in question and give our customers a consistent experience, whether their asset is being overhauled in Malaysia or Brazil.”
GE says the technology could also have applications beyond inspection, such as cleaning, thermal spray and blending operations.GE's open beam x-ray fluorescence spectroscopy device. Credit: GE Aerospace
The STAC will also be the first location at which GE Aerospace deploys a new inspection process for metal parts that uses the same type of technology museums and auction houses utilize to identify forged artwork. GE partnered with scientific instruments company Bruker to develop a non-destructive inspection device that uses open beam x-ray fluorescence spectroscopy (XRF) to detect microstructural variations in metal parts. XRF can provide a view of an object's chemical composition, which in MRO can be used to help a technician more easily spot anomalies in a part. Jenkins says the new inspection technology “will allow us to be even more vigilant with verifying the integrity of metal parts.”
Earlier this summer, GE committed to investing $1 billion over the next five years in its MRO network to support a higher volume of shop visits, reduce turnaround times, upgrade equipment and machines, purchase new tooling, expand and improve facility infrastructure and accelerate repair technology advancement.
In recent years, GE has been developing several interesting robotics and AI-powered technologies for MRO processes. These include a worm-inspired robot that can crawl through the nooks and crannies of jet engine parts to detect defects, AI-enabled fluorescent penetrant and borescope inspections, automated welding technology, and snake-arm robots to provide better access to difficult-to-reach areas of the engine for cleaning, inspection and repair.
Set to open this month near GE's Cincinnati headquarters, the Services Technology Acceleration Center (STAC) will focus on advanced engine inspection, repair and overhaul technologies that the OEM wants to roll out across its global MRO network. According to Nicole Jenkins, chief MRO engineer at GE Aerospace, the facility “will serve as a major accelerator for scaling and deploying cutting edge inspection and repair processes to market.”
One of these technologies will be artificial intelligence (AI) guided white light robot inspections, which aim to ease physical strain on GE's technicians while providing consistency and efficiency benefits. Sam Blazek, services technology leader for white light inspection at GE Aerospace, says he previously had to conduct these types of inspections “caveman style” by hand with a flashlight and mirror, needing to move his head, eyes and neck to manipulate these tools and interpret what he was seeing. “Staring at the same part or feature for 8-12 hr. a day can make your head hurt,” he says.
The new inspection technology uses two articulated industrial robots outfitted with white light optical scanners to carefully move across the surface of a high-precision part, such as a turbine disk. Instead of requiring a human to visually interpret defects such as nicks, dents, scratches and corrosion, the system uses AI to capture and analyze data while creating a digital record of the part's condition. Although the technology automates the inspection itself, technicians will still examine the results on a screen to make a final call about inspection findings and serviceability.
“By using AI and robotics, service engineers can increase the speed and efficiency of part inspections while improving the consistency of their results,” says Jon Hootman, engineering director of the STAC. He adds that the technology is the first time GE has been able to completely digitally capture all characteristics of a part in service and catalog the data throughout its lifetime in a central repository.
“The beauty is that all of this together now pulls in the entire value stream to eradicate inconsistencies in your interpretation,” says Hootman. “[It allows us] to make sure that we are applying the appropriate level of consistency and interpretation to the anomalies in question and give our customers a consistent experience, whether their asset is being overhauled in Malaysia or Brazil.”
GE says the technology could also have applications beyond inspection, such as cleaning, thermal spray and blending operations.GE's open beam x-ray fluorescence spectroscopy device. Credit: GE Aerospace
The STAC will also be the first location at which GE Aerospace deploys a new inspection process for metal parts that uses the same type of technology museums and auction houses utilize to identify forged artwork. GE partnered with scientific instruments company Bruker to develop a non-destructive inspection device that uses open beam x-ray fluorescence spectroscopy (XRF) to detect microstructural variations in metal parts. XRF can provide a view of an object's chemical composition, which in MRO can be used to help a technician more easily spot anomalies in a part. Jenkins says the new inspection technology “will allow us to be even more vigilant with verifying the integrity of metal parts.”
Earlier this summer, GE committed to investing $1 billion over the next five years in its MRO network to support a higher volume of shop visits, reduce turnaround times, upgrade equipment and machines, purchase new tooling, expand and improve facility infrastructure and accelerate repair technology advancement.
In recent years, GE has been developing several interesting robotics and AI-powered technologies for MRO processes. These include a worm-inspired robot that can crawl through the nooks and crannies of jet engine parts to detect defects, AI-enabled fluorescent penetrant and borescope inspections, automated welding technology, and snake-arm robots to provide better access to difficult-to-reach areas of the engine for cleaning, inspection and repair.

Share
Recent Chats
Share via email
Future: handle WhatsApp here
Future: handle LinkedIn here
Future: handle Twitter here
SUBMENU HERE
Share via Chat
Copy Link