New Technologies Drive APU Performance Improvements
Details
More Products & Services
Products & Services
Aerospace | Aviation Week Network
Aviation Week Network
https://aviationweek.com/themes/custom/particle/dist/app-drupal/assets/awn-logo.svg
Home - Aviation Group Marketing
Aviation Week Network
120 data points on over 156,000 commercial and business aviation aircraft, including military transports. Discover the most trustworthy resource for the complete aircraft history, plus ad hoc reports, month-over-month trend analysis and details on expected deliveries through 2050.
People
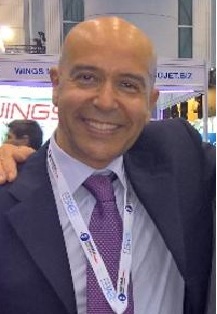
Andrea Rossi Prudente
Aviation Week Network
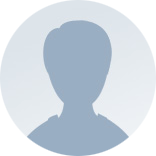
Becca Balmes
Aviation Week Network
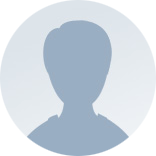
Belinda Tan
Aviation Week Network
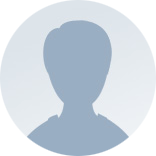
Brian Everstine
Aviation Week Network
Editor
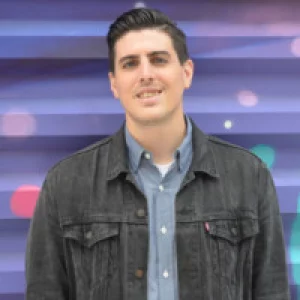
Eddie Krankowski
Aviation Week Network
Assistant Manager, Tradeshows
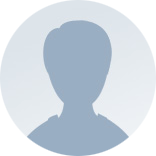
erving dockery
Aviation Week Network
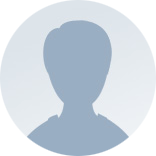
Lisa Tan
Aviation Week Network
Senior Marketing Manager
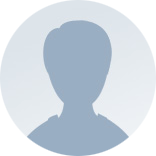
Mark Thomas
Aviation Week Network
Description
Encased in the tail cone of commercial, business, and military aircraft, auxiliary power units enable cabin environmental control system operation without relying on ground power sources. They are also essential for the safety of flight operations such as extended twin-engine operations approvals, main engine restarts and emergency back-up of flight control systems. To enable those functions with greater reliability, auxiliary power unit (APU) technology is being continuously advanced.
One recent example is Honeywell Aerospace Technologies' High Efficiency Mode (HEM) APU upgrade. “The High Efficiency Mode upgrade is the first software-enabled reliability and fuel efficiency upgrade,” says Roy Boyd, Honeywell's senior director of offering management for APUs.
Boyd says the upgrade enables a 2% fuel savings, CO2 savings of 22 metric tons and 1,500 hr. of time on wing reliability per year. The upgrade entails the purchase of a software key that is uploaded to the aircraft for 131-9A APUs, series 25 and above, and 131-9B APUs, series 49 and above. For the prior series 131-9As and 131-9Bs, the APU can be modified at the next major repair shop visit to enable improved fuel savings and time on wing. The modification of the pre-series 25 (9A) or pre-series 49 (9B) will require installation of the new compressor diffuser along with the software key, which is directly loaded into the data memory module through its software loader.
The HEM upgrade was first certified in November 2020 on Airbus A319, A320 and A321 aircraft with the 131-9A APU. In April 2023, Boeing certified HEM on 737-600s, -800s and -900s, and 737 MAXs with the 131-9B APU.
“Since the release of HEM, Honeywell has modified 1,334 APUs, resulting in fuel savings of [approximately 1.8 million] gallons and 17,341 metric tons of CO2,” says Boyd. He adds that along with the retrofit, HEM technology is now included in new production APUs for the Boeing 737 MAX, and the Airbus A319, A320 and A321.Honeywell says its High Efficiency Mode APU upgrade provides 2% fuel savings and saves 22 metric tons of CO2 annually. Credit: Honeywell Aerospace Technologies
In a further development, Boyd reports that Honeywell planned to release a load compressor seal upgrade via service bulletin for the 131-9A APU on the A320 family in September. The load compressor, he explains, provides all the pressurized air for the aircraft's air cycle machines, enabling air conditioning in the main cabin, and additional pneumatic air for secondary systems such as main engine start.
“This upgraded seal design and system will eliminate oil leakage across the compressor seal, further reducing odor in the cabin (OIC) events,” he says. “OIC events are most prevalent on the 131-9A application to the A320 family, which is why the load compressor seal upgrade will be specific to that APU.”
Boyd says Honeywell is also in the final development stages of the 331-500B2 APU for the new Boeing 777X. The 331-500B2 incorporates new updates qualifying it to the latest fire resistance and fireproof certification in the industry. He says additional technology focuses on improved software that enables improved cycling cool-down and de-oiling functions, and an improved starter and ignition system.
APU TRENDS
APU on-wing trend monitoring has taken off over the past couple of years, according to Roger Willis, APU program director at StandardAero's Maryville, Tennessee facility.
“This allows for better troubleshooting and reduced downtime on the aircraft, along with a reduction in the carrying cost associated with spare APU line replacement units (LRU) and spare APUs to cover failures or removals,” says Willis, noting that LRUs and life-limited components (LLC) drive the majority of APU removals. “With trend monitoring, there is better planning of scheduled and unscheduled removals regarding LLCs. For LRUs, new service bulletins to increase on-wing time have been developed.”StandardAero says APU on-wing monitoring has taken off over the past few years. Credit: StandardAero
Willis says APU trend monitoring has shown an 8-10% improvement in on-wing reliability over the past 3 years, depending on the model. He says this is also largely due to new repair development utilizing material improvements, plus service bulletin modifications to the APU and/or its LRUs.
“Service bulletins are issued regularly, driving improvements on current APU units, but there is also an increasing number of items—such as the outer ducts—on APUs that are made of lighter material such as carbon fiber, which help to reduce weight,” says Willis.
Asked about any trends toward smaller APUs, Willis says that he has not seen a noticeable change in size among new-generation APU designs. “New-generation APUs and upgrades to existing APUs tend to be focused on reductions in fuel consumption and emissions,” he says.
Chap Berrier, vice president of global sales at APU MRO specialist Tag Aero, reports that different metals and OEM-proprietary coatings are now being applied to the APU hot section. “In addition to the hot section, the new metals and coatings upgrades are being applied to turbine wheels and the compressor, among other life-limited parts,” he says.
Berrier also attributes greater on-wing longevity to the anti-erosion properties of those coatings and metals, due to their resistance to the extreme temperatures of hot gas. “Aircraft technology is getting better at monitoring the health of the APUs, of which one of the key indicators is exhaust gas temperature,” he says. “That is a good indicator as to how well the APU is performing.”
NEW TECHNOLOGY OPPORTUNITIES
Ole Gosau, head of APU services at Lufthansa Technik, says that in recent years, APU OEMs have put more emphasis on continuous product improvements rather than on disruptive solutions, such as novel architectures or new technological or engineering approaches.
“Generally, the industry is sticking to the proven radial gas turbine architectures, stabilizing the reliability and extending the on-wing times,” he says. “Moreover, the implementation of service bulletins and the eradication of known weaknesses have been among the priorities.”
As a result, Gosau says APU innovations have been taking place at a smaller scale, concentrating on parts coatings technology, the rotor system and more advanced materials.Tag Aero says different metals and OEM-proprietary coatings are now being applied to the APU hot section. Credit: Tag Aero
“We are seeing an increased percentage of titanium parts for the impellers and three stages of turbine blades for the larger APUs as examples,” he says. “Newer APU types have, on the one hand, made noteworthy progress over legacy types, for instance, when it comes to improving the time-on wing or reducing the occurrence of oil smell events. On the other hand, the achieved benefits were usually accompanied by a significant increase in material prices.”
When asked if APU OEMs might introduce any radically new technology, Gosau says he does not foresee a near-term replacement of the current generation APU systems architectures. “Things might change with new aircraft propulsion architectures, which, in my opinion, are still at least a decade and a half away,” he says. “One—but not the only one—could be hydrogen. In the meantime, as a stop-gap solution, APUs can be fueled with the same sustainable aviation fuels as the main turbofan engines.”
APU power derived from a hydrogen fuel cell is not out of the question. Emissions, noise, fuel and maintenance reduction would be its advantages, explains Jenny Kavanagh, chief strategy officer at Cranfield Aerospace Solutions in the UK.
“Conventionally powered APUs have been reported to contribute 20% of all aircraft on ground emissions and up to 10% of all aircraft emissions at airports. Hydrogen fuel cells only emit water, providing a completely clean solution,” says Kavanagh. “Although hydrogen is more expensive (at least for now) than kerosene, you need a lot less of it due to the higher efficiency of fuel cells versus gas turbines, as well as the higher energy density of hydrogen.
“In addition, hydrogen fuel cells have a much higher period between overhauls, meaning the reliability is higher and maintenance costs are reduced,” says Kavanaugh. She adds that hydrogen fuel cells are relatively silent, citing APUs as one of the largest contributors to ramp and gate noise at airports.
Kavanaugh says Cranfield has identified specific challenges related to the installation of a hydrogen APU in a conventionally powered aircraft. “Current fuel cell technology takes up a lot of space and therefore any hydrogen fuel cell system used as an APU would need to be packaged in a way that would allow it to fit into the aircraft APU bay in the tail,” she says. “[Cranfield] has already solved this challenge. Weight will also be a challenge, but our initial assessments show this is manageable.”
One recent example is Honeywell Aerospace Technologies' High Efficiency Mode (HEM) APU upgrade. “The High Efficiency Mode upgrade is the first software-enabled reliability and fuel efficiency upgrade,” says Roy Boyd, Honeywell's senior director of offering management for APUs.
Boyd says the upgrade enables a 2% fuel savings, CO2 savings of 22 metric tons and 1,500 hr. of time on wing reliability per year. The upgrade entails the purchase of a software key that is uploaded to the aircraft for 131-9A APUs, series 25 and above, and 131-9B APUs, series 49 and above. For the prior series 131-9As and 131-9Bs, the APU can be modified at the next major repair shop visit to enable improved fuel savings and time on wing. The modification of the pre-series 25 (9A) or pre-series 49 (9B) will require installation of the new compressor diffuser along with the software key, which is directly loaded into the data memory module through its software loader.
The HEM upgrade was first certified in November 2020 on Airbus A319, A320 and A321 aircraft with the 131-9A APU. In April 2023, Boeing certified HEM on 737-600s, -800s and -900s, and 737 MAXs with the 131-9B APU.
“Since the release of HEM, Honeywell has modified 1,334 APUs, resulting in fuel savings of [approximately 1.8 million] gallons and 17,341 metric tons of CO2,” says Boyd. He adds that along with the retrofit, HEM technology is now included in new production APUs for the Boeing 737 MAX, and the Airbus A319, A320 and A321.Honeywell says its High Efficiency Mode APU upgrade provides 2% fuel savings and saves 22 metric tons of CO2 annually. Credit: Honeywell Aerospace Technologies
In a further development, Boyd reports that Honeywell planned to release a load compressor seal upgrade via service bulletin for the 131-9A APU on the A320 family in September. The load compressor, he explains, provides all the pressurized air for the aircraft's air cycle machines, enabling air conditioning in the main cabin, and additional pneumatic air for secondary systems such as main engine start.
“This upgraded seal design and system will eliminate oil leakage across the compressor seal, further reducing odor in the cabin (OIC) events,” he says. “OIC events are most prevalent on the 131-9A application to the A320 family, which is why the load compressor seal upgrade will be specific to that APU.”
Boyd says Honeywell is also in the final development stages of the 331-500B2 APU for the new Boeing 777X. The 331-500B2 incorporates new updates qualifying it to the latest fire resistance and fireproof certification in the industry. He says additional technology focuses on improved software that enables improved cycling cool-down and de-oiling functions, and an improved starter and ignition system.
APU TRENDS
APU on-wing trend monitoring has taken off over the past couple of years, according to Roger Willis, APU program director at StandardAero's Maryville, Tennessee facility.
“This allows for better troubleshooting and reduced downtime on the aircraft, along with a reduction in the carrying cost associated with spare APU line replacement units (LRU) and spare APUs to cover failures or removals,” says Willis, noting that LRUs and life-limited components (LLC) drive the majority of APU removals. “With trend monitoring, there is better planning of scheduled and unscheduled removals regarding LLCs. For LRUs, new service bulletins to increase on-wing time have been developed.”StandardAero says APU on-wing monitoring has taken off over the past few years. Credit: StandardAero
Willis says APU trend monitoring has shown an 8-10% improvement in on-wing reliability over the past 3 years, depending on the model. He says this is also largely due to new repair development utilizing material improvements, plus service bulletin modifications to the APU and/or its LRUs.
“Service bulletins are issued regularly, driving improvements on current APU units, but there is also an increasing number of items—such as the outer ducts—on APUs that are made of lighter material such as carbon fiber, which help to reduce weight,” says Willis.
Asked about any trends toward smaller APUs, Willis says that he has not seen a noticeable change in size among new-generation APU designs. “New-generation APUs and upgrades to existing APUs tend to be focused on reductions in fuel consumption and emissions,” he says.
Chap Berrier, vice president of global sales at APU MRO specialist Tag Aero, reports that different metals and OEM-proprietary coatings are now being applied to the APU hot section. “In addition to the hot section, the new metals and coatings upgrades are being applied to turbine wheels and the compressor, among other life-limited parts,” he says.
Berrier also attributes greater on-wing longevity to the anti-erosion properties of those coatings and metals, due to their resistance to the extreme temperatures of hot gas. “Aircraft technology is getting better at monitoring the health of the APUs, of which one of the key indicators is exhaust gas temperature,” he says. “That is a good indicator as to how well the APU is performing.”
NEW TECHNOLOGY OPPORTUNITIES
Ole Gosau, head of APU services at Lufthansa Technik, says that in recent years, APU OEMs have put more emphasis on continuous product improvements rather than on disruptive solutions, such as novel architectures or new technological or engineering approaches.
“Generally, the industry is sticking to the proven radial gas turbine architectures, stabilizing the reliability and extending the on-wing times,” he says. “Moreover, the implementation of service bulletins and the eradication of known weaknesses have been among the priorities.”
As a result, Gosau says APU innovations have been taking place at a smaller scale, concentrating on parts coatings technology, the rotor system and more advanced materials.Tag Aero says different metals and OEM-proprietary coatings are now being applied to the APU hot section. Credit: Tag Aero
“We are seeing an increased percentage of titanium parts for the impellers and three stages of turbine blades for the larger APUs as examples,” he says. “Newer APU types have, on the one hand, made noteworthy progress over legacy types, for instance, when it comes to improving the time-on wing or reducing the occurrence of oil smell events. On the other hand, the achieved benefits were usually accompanied by a significant increase in material prices.”
When asked if APU OEMs might introduce any radically new technology, Gosau says he does not foresee a near-term replacement of the current generation APU systems architectures. “Things might change with new aircraft propulsion architectures, which, in my opinion, are still at least a decade and a half away,” he says. “One—but not the only one—could be hydrogen. In the meantime, as a stop-gap solution, APUs can be fueled with the same sustainable aviation fuels as the main turbofan engines.”
APU power derived from a hydrogen fuel cell is not out of the question. Emissions, noise, fuel and maintenance reduction would be its advantages, explains Jenny Kavanagh, chief strategy officer at Cranfield Aerospace Solutions in the UK.
“Conventionally powered APUs have been reported to contribute 20% of all aircraft on ground emissions and up to 10% of all aircraft emissions at airports. Hydrogen fuel cells only emit water, providing a completely clean solution,” says Kavanagh. “Although hydrogen is more expensive (at least for now) than kerosene, you need a lot less of it due to the higher efficiency of fuel cells versus gas turbines, as well as the higher energy density of hydrogen.
“In addition, hydrogen fuel cells have a much higher period between overhauls, meaning the reliability is higher and maintenance costs are reduced,” says Kavanaugh. She adds that hydrogen fuel cells are relatively silent, citing APUs as one of the largest contributors to ramp and gate noise at airports.
Kavanaugh says Cranfield has identified specific challenges related to the installation of a hydrogen APU in a conventionally powered aircraft. “Current fuel cell technology takes up a lot of space and therefore any hydrogen fuel cell system used as an APU would need to be packaged in a way that would allow it to fit into the aircraft APU bay in the tail,” she says. “[Cranfield] has already solved this challenge. Weight will also be a challenge, but our initial assessments show this is manageable.”

Share
Recent Chats
Share via email
Future: handle WhatsApp here
Future: handle LinkedIn here
Future: handle Twitter here
SUBMENU HERE
Share via Chat
Copy Link