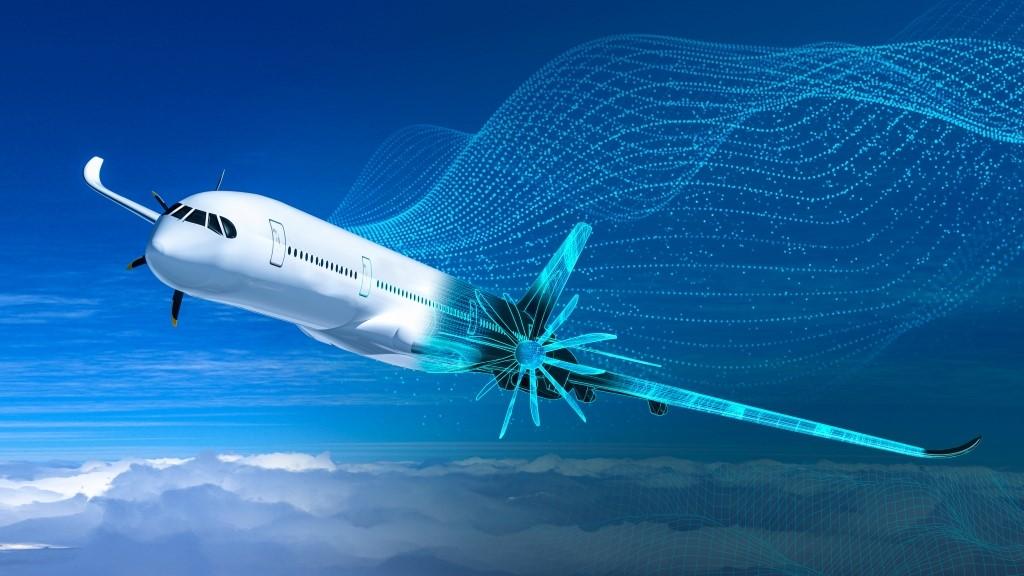
How Airbus Atlantic Is Employing Industrial Transformation As A Strategic Lever
How Airbus Atlantic Is Employing Industrial Transformation As A Strategic Lever
Details
More Products & Services
Products & Services
Aerospace | Aviation Week Network
Aviation Week Network
https://aviationweek.com/themes/custom/particle/dist/app-drupal/assets/awn-logo.svg
Home - Aviation Group Marketing
Aviation Week Network
120 data points on over 156,000 commercial and business aviation aircraft, including military transports. Discover the most trustworthy resource for the complete aircraft history, plus ad hoc reports, month-over-month trend analysis and details on expected deliveries through 2050.
People
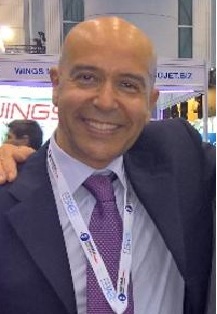
Andrea Rossi Prudente
Aviation Week Network
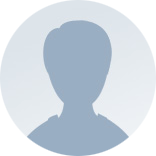
Becca Balmes
Aviation Week Network
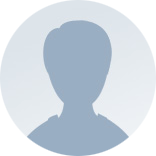
Belinda Tan
Aviation Week Network
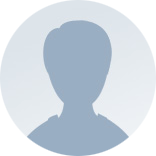
Brian Everstine
Aviation Week Network
Editor
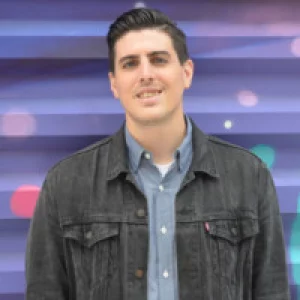
Eddie Krankowski
Aviation Week Network
Assistant Manager, Tradeshows
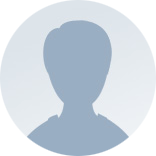
erving dockery
Aviation Week Network
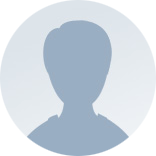
Lisa Tan
Aviation Week Network
Senior Marketing Manager
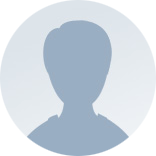
Mark Thomas
Aviation Week Network
Description
A supply chain disrupted by the Covid-19 pandemic and an increase in orders are prompting Airbus Atlantic, the industrial aerostructure arm of the Airbus group, to rethink its production system through its ambitious "Industry of the Future" program. Bruno Rameau, the leader of R&D industrial partners of this program, discusses its motivations and the importance of technology collaboration.
Airbus Atlantic employs more than 13,500 employees, spread over 15 sites located in five countries on three continents. Suffice to say that the transformation of the aerospace industry giant's production system is a huge challenge.
This change, which is necessarily systemic, "involves adapting our production process to allow the rapid ramp-up of complex and innovative products, while maintaining our quality standards at the highest level. We also need to strengthen our resilience in the face of events that are as inevitable as they are unforeseen, as the Covid-19 crisis has taught us," says Bruno Rameau, Head of R&D Operations & Strategy at Airbus Atlantic.
The added challenges of decarbonization, increases the pitfalls. "Airbus is at the forefront of developing a new generation of zero-emission aircraft," says Bruno Rameau. The "Industry of the Future" program, which will run over a period of ten years, was launched with the support of the French Civil Aviation Authority (DGAC), through the Aeronautics Recovery Fund under its CORAC initiative.
The program simultaneously touches on the way space is used in production sites, production processes, the introduction of new manufacturing processes and the adaptation of its supply chain. This important supply chain aspect includes procedures to organize information exchange and collaboration between Airbus Atlantic and its partners – including suppliers of raw materials, aircraft sub-assemblies or technology. In other words, it covers all industrial subjects: new paradigms for product design and process development; production of metal or composite parts; assembly and integration technologies; systems and equipment used by workers; quality management and logistics.
The six pillars of the action plan
Bruno Rameau states that Airbus Atlantic's action plan is based on six pillars:The implementation of a digital thread between the aircraft manufacturer and supply chain partnersThe deployment of a robust and reliable production system built on technologies such as IoT, big data and artificial intelligence in a secure environmentThe reduction of aircraft weight and the use of less energy-intensive processes based on disruptive technologiesThe use of more flexible and efficient aerostructure assembly systems through simulation, automation and robotics that will replace massive tooling and manual operations that have low added valueEnabling new forms of collaboration across the entire supply chain to ensure the overall performance of the complete value chainMaintaining a close partnership with customers to continue to mature the essential technology building blocks.
Key Technology Partners
To move faster in its transformation, Airbus Atlantic has chosen to rely on technology partners that are recognized in their field. Hexagon's PRESTO automated quality inspection cell inspecting a fuselage panel
Among them, Hexagon brings skills in metrology, simulation and digital twins that includes:Employing digital twins of machine tools to train operators with hardware simulators using critical scenarios, and to facilitate the industrialization of new parts with faster implementation time and improved part quality rejection rates.The 100% automated measurement and quality control of parts (e.g. welding on tubes, geometry of the shape of panels coming out of machines) to digitize every part and enable quality improvement.Employing virtual assembly processes to predict and mitigate integration issues before operations begin, facilitating high-speed and confident ramp-up of aircraft production.
"By 2026, industrial demonstrators of these new systems will be immersed in our workshops in order to adapt them to our needs and give operators time to train. This phase will be followed by a gradual integration of the tested solutions, into both our factories and at those of "flying" parts suppliers. The distribution of the new systems and equipment will extend to both our direct partners and our partners' partners," says Bruno Rameau.
According to Airbus Atlantic, some actions have already led to the successful achievement of higher production rates, combined with high levels of quality and enhanced competitiveness. The "Industry of the Future" program has undoubtedly taken off.
Airbus Atlantic employs more than 13,500 employees, spread over 15 sites located in five countries on three continents. Suffice to say that the transformation of the aerospace industry giant's production system is a huge challenge.
This change, which is necessarily systemic, "involves adapting our production process to allow the rapid ramp-up of complex and innovative products, while maintaining our quality standards at the highest level. We also need to strengthen our resilience in the face of events that are as inevitable as they are unforeseen, as the Covid-19 crisis has taught us," says Bruno Rameau, Head of R&D Operations & Strategy at Airbus Atlantic.
The added challenges of decarbonization, increases the pitfalls. "Airbus is at the forefront of developing a new generation of zero-emission aircraft," says Bruno Rameau. The "Industry of the Future" program, which will run over a period of ten years, was launched with the support of the French Civil Aviation Authority (DGAC), through the Aeronautics Recovery Fund under its CORAC initiative.
The program simultaneously touches on the way space is used in production sites, production processes, the introduction of new manufacturing processes and the adaptation of its supply chain. This important supply chain aspect includes procedures to organize information exchange and collaboration between Airbus Atlantic and its partners – including suppliers of raw materials, aircraft sub-assemblies or technology. In other words, it covers all industrial subjects: new paradigms for product design and process development; production of metal or composite parts; assembly and integration technologies; systems and equipment used by workers; quality management and logistics.
The six pillars of the action plan
Bruno Rameau states that Airbus Atlantic's action plan is based on six pillars:The implementation of a digital thread between the aircraft manufacturer and supply chain partnersThe deployment of a robust and reliable production system built on technologies such as IoT, big data and artificial intelligence in a secure environmentThe reduction of aircraft weight and the use of less energy-intensive processes based on disruptive technologiesThe use of more flexible and efficient aerostructure assembly systems through simulation, automation and robotics that will replace massive tooling and manual operations that have low added valueEnabling new forms of collaboration across the entire supply chain to ensure the overall performance of the complete value chainMaintaining a close partnership with customers to continue to mature the essential technology building blocks.
Key Technology Partners
To move faster in its transformation, Airbus Atlantic has chosen to rely on technology partners that are recognized in their field. Hexagon's PRESTO automated quality inspection cell inspecting a fuselage panel
Among them, Hexagon brings skills in metrology, simulation and digital twins that includes:Employing digital twins of machine tools to train operators with hardware simulators using critical scenarios, and to facilitate the industrialization of new parts with faster implementation time and improved part quality rejection rates.The 100% automated measurement and quality control of parts (e.g. welding on tubes, geometry of the shape of panels coming out of machines) to digitize every part and enable quality improvement.Employing virtual assembly processes to predict and mitigate integration issues before operations begin, facilitating high-speed and confident ramp-up of aircraft production.
"By 2026, industrial demonstrators of these new systems will be immersed in our workshops in order to adapt them to our needs and give operators time to train. This phase will be followed by a gradual integration of the tested solutions, into both our factories and at those of "flying" parts suppliers. The distribution of the new systems and equipment will extend to both our direct partners and our partners' partners," says Bruno Rameau.
According to Airbus Atlantic, some actions have already led to the successful achievement of higher production rates, combined with high levels of quality and enhanced competitiveness. The "Industry of the Future" program has undoubtedly taken off.

Share
Recent Chats
Share via email
Future: handle WhatsApp here
Future: handle LinkedIn here
Future: handle Twitter here
SUBMENU HERE
Share via Chat
Copy Link