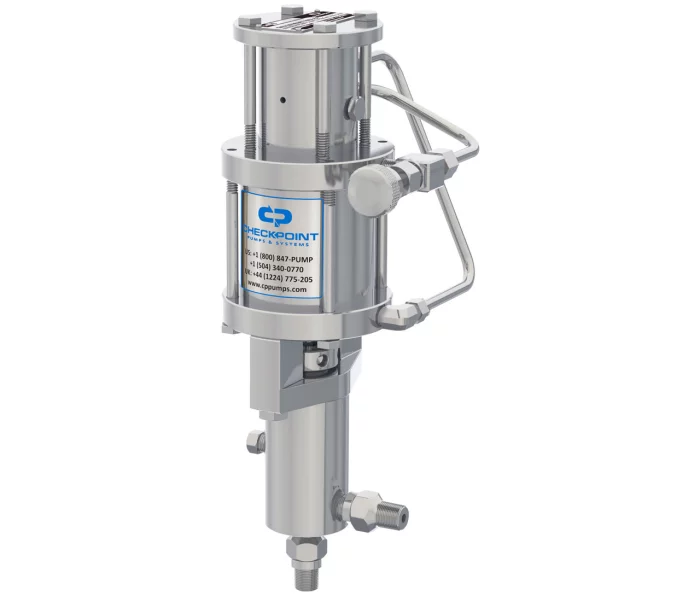
Pneumatic Pump Series 1250
SUPERIOR DESIGN
No Springs or Diaphragms, • Durable, High-Quality Materials
CHEMICAL RESISTANCE
Proprietary, high-quality seal materials enable CheckPoint pumps to provide unparalleled chemical re
WARRANTY
CheckPoint guarantees 40 months of material and workmanship.
OPTIONS
GR:Gas recovery capability EV: Extreme Viscosity
CheckPoint’s Series 1250 pump delivers up to 8 USG/H (30.38 L/H) and can reliably inject into pressures up to 12,000 PSIG (827.4 BARG).
PUMP CATEGORY :
Type: Plunger Control: Cycle Speed Stroke: 1in (25mm) Fixed
FLOW RATE :
0.002 - 8.0 USG/H (0.007 - 30.28 L/H)
PRESSURE :
0 - 12,000 PSIG (0 - 827.4 BARG)
SUPERIOR DESIGN :
No Springs or Diaphragms • Accurate and Repeatable Injection Durable, High-Quality Materials
CHEMICAL RESISTANCE :
Proprietary, high-quality seal materials enable CheckPoint pumps to provide unparalleled chemical re
Description
More Products & Services
Products & Services
Solar Series FXS
checkpoint Pumps & Systems
CheckPoint’s Series FXS Solar Injection System was designed to provide a quality,low-maintenance,and environmentally friendly chemical injection solution.From its high-grade materials of construction (316SS,Hastelloy,and PVC)to its unique tripod stand, this system was designed with maximum utility in mind.
The Series FXS Solar Injection System’s lightweight,portable,and sturdy design lends itself to easy mobility in the field.Each system is prewired with industry-standard MC4 quick connectors For both the panel and the pump,ensuring minimal installation and setup time.The entire system was designed to be effortlessly assembled by one person in as little as fifteen minutes.The front access enclosure containing its battery and charge controller is raised to an easy-access level that provides clearance for rain or snow.The integrated base allows the pump to dependably stand alone or to be easily bolted to a structure.
This package can accommodate multiple plunger diameters ranging from 1/8” to 1/2”,which allows for a wide variety of flow rates and pressures. The pump can deliver up to 552.3 USG/D(1920.23 L/D) and can reliably inject into pressures up to 12,000PSIG(827.37 BARG).
CheckPoint’s Series FXS Solar Injection System is optimized for continuous,reliable chemical injection,with precision flow rate control and no timers.Its Class1, Division2 pump motor ensures a heightened level of quality and safety. Each solar system is sized per application and uses a highly efficient pump designed and manufactured in-house by CheckPoint, ensuring battery longevity.In addition to diminishing the waste associated with battery failure, eliminating gas emissions further protects the environment.
From its ease of installation and maintenance, to its wide range of flow rates and pressures, to its safety
and environmental benefits, every aspect of this system’s design will optimize your chemical injection processes. For applications beyond those provided, please contact CheckPoint for a customized solution.
The Series FXS Solar Injection System’s lightweight,portable,and sturdy design lends itself to easy mobility in the field.Each system is prewired with industry-standard MC4 quick connectors For both the panel and the pump,ensuring minimal installation and setup time.The entire system was designed to be effortlessly assembled by one person in as little as fifteen minutes.The front access enclosure containing its battery and charge controller is raised to an easy-access level that provides clearance for rain or snow.The integrated base allows the pump to dependably stand alone or to be easily bolted to a structure.
This package can accommodate multiple plunger diameters ranging from 1/8” to 1/2”,which allows for a wide variety of flow rates and pressures. The pump can deliver up to 552.3 USG/D(1920.23 L/D) and can reliably inject into pressures up to 12,000PSIG(827.37 BARG).
CheckPoint’s Series FXS Solar Injection System is optimized for continuous,reliable chemical injection,with precision flow rate control and no timers.Its Class1, Division2 pump motor ensures a heightened level of quality and safety. Each solar system is sized per application and uses a highly efficient pump designed and manufactured in-house by CheckPoint, ensuring battery longevity.In addition to diminishing the waste associated with battery failure, eliminating gas emissions further protects the environment.
From its ease of installation and maintenance, to its wide range of flow rates and pressures, to its safety
and environmental benefits, every aspect of this system’s design will optimize your chemical injection processes. For applications beyond those provided, please contact CheckPoint for a customized solution.
ELECTRIC PUMP SERIES SLA Leakless
checkpoint Pumps & Systems
CheckPoint’s New LeakLess Head Technology boasts surprising results for even the most seasoned pump
experts. Tested to more than 100 million strokes yet the seals did not reach failure. The LeakLess design was
initially engineered to answer the industry’s historical appreciation for diaphragm pumps, while hoping for
higher pressures and more consistent injection volumes. The product exceeded its goals and now stands to
revolutionize CheckPoint's Patented products beyond even this model release. Paired with the Series SLA electric
drive, the pump delivers up to 50.87 USG/H (192.56 L/H) and can reliably inject into pressures up to 13,500 PSIG
(931 BARG) per head. It features a robust casing and a variable eccentric drive designed to withstand
harsh conditions of oil and gas installations, and it contains minimal moving parts to further guarantee
long-term reliability and superior uptime. The Series SLA electric pump's controlled volume pump
specifications and high metering accuracy meet or exceed API674 and 675 standards. A nearly infinitely
adjustable stroke length of 0-1 in (0-25.4 mm) ensures extremely precise and accurate dosing and a large
turndown ratio of 10:1*. The flow rate can be controlled while the unit is stopped or running by a single
hand with the manual Vernier scale dial. Optional rotary actuators are available to allow for remote rate
control, can be used on each injection head independently for multi-injection service and are available in many
area classifications and control signal types. Multiple drives may be combined with one motor to provide
redundancy, or to service several injection points. This feature aids in minimizing cost, footprint, and
weight, while maintaining a high degree of accuracy at each individual point regardless of differences in
operating pressures. CheckPoint’s Series SLA drives can be coupled, and a large selection of motors can be
accommodated. The design of this electric pump provides a wide variety of solutions and ensures compliance
to any electrical requirements. To meet a wide array of chemical injection applications and to reduce
spares inventory through part interchange-ability, Series SLA pumps utilize CheckPoint’s distinguished
LeakLess modular chemical heads, which offer a full range of plunger diameters from 1/8" to 1-1/2".
Our pumps maintain unparalleled chemical resistance due to the essential integration of high-quality,
proprietary seal materials. In order to meet a wide variety of chemical compatibility needs, wetted parts are
available in an array of materials, such as 316 SS, Hastelloy C-276, Duplex 2205, Super Duplex 2507, PVC, ceramic
and titanium, and seals are available in Viton, HNBR, FKM, and FFKM. All wet end construction materials meet
the requirements of NACE MR0175 and ISO 15156.
experts. Tested to more than 100 million strokes yet the seals did not reach failure. The LeakLess design was
initially engineered to answer the industry’s historical appreciation for diaphragm pumps, while hoping for
higher pressures and more consistent injection volumes. The product exceeded its goals and now stands to
revolutionize CheckPoint's Patented products beyond even this model release. Paired with the Series SLA electric
drive, the pump delivers up to 50.87 USG/H (192.56 L/H) and can reliably inject into pressures up to 13,500 PSIG
(931 BARG) per head. It features a robust casing and a variable eccentric drive designed to withstand
harsh conditions of oil and gas installations, and it contains minimal moving parts to further guarantee
long-term reliability and superior uptime. The Series SLA electric pump's controlled volume pump
specifications and high metering accuracy meet or exceed API674 and 675 standards. A nearly infinitely
adjustable stroke length of 0-1 in (0-25.4 mm) ensures extremely precise and accurate dosing and a large
turndown ratio of 10:1*. The flow rate can be controlled while the unit is stopped or running by a single
hand with the manual Vernier scale dial. Optional rotary actuators are available to allow for remote rate
control, can be used on each injection head independently for multi-injection service and are available in many
area classifications and control signal types. Multiple drives may be combined with one motor to provide
redundancy, or to service several injection points. This feature aids in minimizing cost, footprint, and
weight, while maintaining a high degree of accuracy at each individual point regardless of differences in
operating pressures. CheckPoint’s Series SLA drives can be coupled, and a large selection of motors can be
accommodated. The design of this electric pump provides a wide variety of solutions and ensures compliance
to any electrical requirements. To meet a wide array of chemical injection applications and to reduce
spares inventory through part interchange-ability, Series SLA pumps utilize CheckPoint’s distinguished
LeakLess modular chemical heads, which offer a full range of plunger diameters from 1/8" to 1-1/2".
Our pumps maintain unparalleled chemical resistance due to the essential integration of high-quality,
proprietary seal materials. In order to meet a wide variety of chemical compatibility needs, wetted parts are
available in an array of materials, such as 316 SS, Hastelloy C-276, Duplex 2205, Super Duplex 2507, PVC, ceramic
and titanium, and seals are available in Viton, HNBR, FKM, and FFKM. All wet end construction materials meet
the requirements of NACE MR0175 and ISO 15156.
ELECTRIC PUMP SERIES SLA
checkpoint Pumps & Systems
CheckPoint’s Series SLA electric plunger pump delivers up to 50.87 USG/H (192.56 L/H) and can reliably
inject into pressures up to 13,500 PSIG (931 BARG) per head. It features a robust casing and a variable
eccentric drive designed to withstand harsh conditions of oil and gas installations, and it contains minimal
moving parts to further guarantee long-term reliability and superior uptime. The Series SLA electric pump's
controlled volume pump specifications and high metering accuracy meet API675 standards. A nearly
infinitely adjustable stroke length of 0-1 in (0-25.4 mm) ensures extremely precise and accurate dosing and
a large turndown ratio of 10:1*
. The flow rate can be controlled while the unit is stopped or running by a
single hand with the manual Vernier scale dial. Multiple drives may be combined with one motor to
provide redundancy, or to service several injection points. This feature aids in minimizing cost, footprint,
and weight, while maintaining a high degree of accuracy at each individual point regardless of differences
in operating pressures. CheckPoint’s Series SLA drives can be coupled, and a large selection of motors can
be accommodated. The design of this electric pump provides a wide variety of solutions and ensures
compliance to any electrical requirements. To meet a wide array of chemical injection applications and to
reduce spares inventory through part interchange-ability, Series SLA pumps utilize CheckPoint’s
distinguished Series 1500 modular chemical heads, which offer a full range of plunger diameters from 3/8"
to 1-1/2".
Our pumps maintain unparalleled chemical resistance due to the essential integration of high-quality, proprietary seal materials. In order to meet a wide variety of chemical compatibility needs, wetted parts are
available in an array of materials, such as 316 SS, Hastelloy C-276, Duplex 2205, Super Duplex 2507, PVC,
ceramic and titanium, and seals are available in Viton, HNBR, FKM, and FFKM. All wet end construction
materials meet the requirements of NACE MR0175 and ISO 15156.
inject into pressures up to 13,500 PSIG (931 BARG) per head. It features a robust casing and a variable
eccentric drive designed to withstand harsh conditions of oil and gas installations, and it contains minimal
moving parts to further guarantee long-term reliability and superior uptime. The Series SLA electric pump's
controlled volume pump specifications and high metering accuracy meet API675 standards. A nearly
infinitely adjustable stroke length of 0-1 in (0-25.4 mm) ensures extremely precise and accurate dosing and
a large turndown ratio of 10:1*
. The flow rate can be controlled while the unit is stopped or running by a
single hand with the manual Vernier scale dial. Multiple drives may be combined with one motor to
provide redundancy, or to service several injection points. This feature aids in minimizing cost, footprint,
and weight, while maintaining a high degree of accuracy at each individual point regardless of differences
in operating pressures. CheckPoint’s Series SLA drives can be coupled, and a large selection of motors can
be accommodated. The design of this electric pump provides a wide variety of solutions and ensures
compliance to any electrical requirements. To meet a wide array of chemical injection applications and to
reduce spares inventory through part interchange-ability, Series SLA pumps utilize CheckPoint’s
distinguished Series 1500 modular chemical heads, which offer a full range of plunger diameters from 3/8"
to 1-1/2".
Our pumps maintain unparalleled chemical resistance due to the essential integration of high-quality, proprietary seal materials. In order to meet a wide variety of chemical compatibility needs, wetted parts are
available in an array of materials, such as 316 SS, Hastelloy C-276, Duplex 2205, Super Duplex 2507, PVC,
ceramic and titanium, and seals are available in Viton, HNBR, FKM, and FFKM. All wet end construction
materials meet the requirements of NACE MR0175 and ISO 15156.
Pneumatic Pump Series 8400
checkpoint Pumps & Systems
From the isolated chemical head to the switching valve to the materials of construction, CheckPoint’s Series
8400 pump was developed for continuous, accurate, and reliable injection in harsh offshore and remote
locations. No compromises were made. We designed this pump for vital, mission-critical chemicals like
methanol, drag reducer, and other expensive, hazardous, and corrosive production compounds.
In order to meet a wide variety of chemical compatibility needs, wetted parts are available in an array of
materials, such as 316 SS, Hastelloy C-276, Duplex 2205, Super Duplex 2507, ceramic and titanium, and
seals are available in Viton, HNBR, FKM, and FFKM. All construction materials are compatible with sour
gas according to NACE MRO175 and ISO 15156. CheckPoint pumps do not contain any springs and have
fewer moving parts than any other pneumatic pump in the industry, resulting in minimal wear, effective
maintenance, and ultimately an increased life span.
Our pneumatic pumps can recover exhaust gas, even under significant backpressure. This unique gas
recovery system enables processes to reuse drive gas after it has powered the pump. Consider the
environmental benefits, as well as the cost savings, achieved by rerouting spent drive gas to the suction side
of a gas compressor. This exclusive feature aids in lowering gas emissions while powering thermoelectric
generators, feeding catalytic heaters, and even running within enclosures while venting externally
8400 pump was developed for continuous, accurate, and reliable injection in harsh offshore and remote
locations. No compromises were made. We designed this pump for vital, mission-critical chemicals like
methanol, drag reducer, and other expensive, hazardous, and corrosive production compounds.
In order to meet a wide variety of chemical compatibility needs, wetted parts are available in an array of
materials, such as 316 SS, Hastelloy C-276, Duplex 2205, Super Duplex 2507, ceramic and titanium, and
seals are available in Viton, HNBR, FKM, and FFKM. All construction materials are compatible with sour
gas according to NACE MRO175 and ISO 15156. CheckPoint pumps do not contain any springs and have
fewer moving parts than any other pneumatic pump in the industry, resulting in minimal wear, effective
maintenance, and ultimately an increased life span.
Our pneumatic pumps can recover exhaust gas, even under significant backpressure. This unique gas
recovery system enables processes to reuse drive gas after it has powered the pump. Consider the
environmental benefits, as well as the cost savings, achieved by rerouting spent drive gas to the suction side
of a gas compressor. This exclusive feature aids in lowering gas emissions while powering thermoelectric
generators, feeding catalytic heaters, and even running within enclosures while venting externally
ELECTRIC PUMP SERIES ATP
checkpoint Pumps & Systems
CheckPoint's Series ATP3 is an economical electric pump solution with diverse capabilities,
both onshore and offshore. Well-suited for solar, AC, and DC service, this pump
features expandability to two heads, each with mechanical adjustment offering independent
flow control from 0 to 100%. The Series ATP3's robust drive mechanism ensures minimal
wear, smooth operation, and long-term durability. This versatile pump features advanced
head technology, which includes an enclosed, nonadjustable seal, interior wipers,
no backside suction, and additional seal protection, providing increased protection
from water and dust ingress. The nonadjustable seal further protects the pump
by preventing premature seal wear and unnecessary user error, such as over-tightening
packing. Selecting the double-headed configuration provides an opportunity to reduce the
chemical injection solution's footprint and optimize efficiency by utilizing a single motor for
twice the injection capability. Flow efficiency is further maximized by bubble-tight check valves.
CheckPoint engineers designed this pump with field efficiency in mind. The included stand ensures that
the pump can be easily placed directly onto the ground or over existing tank containment basins;
however, in the event that the stand is not needed, it can be easily removed and stored. Together, the
Series ATP and its stand provide a quality, effective, and convenient chemical injection solution for a wide
variety of applications.
both onshore and offshore. Well-suited for solar, AC, and DC service, this pump
features expandability to two heads, each with mechanical adjustment offering independent
flow control from 0 to 100%. The Series ATP3's robust drive mechanism ensures minimal
wear, smooth operation, and long-term durability. This versatile pump features advanced
head technology, which includes an enclosed, nonadjustable seal, interior wipers,
no backside suction, and additional seal protection, providing increased protection
from water and dust ingress. The nonadjustable seal further protects the pump
by preventing premature seal wear and unnecessary user error, such as over-tightening
packing. Selecting the double-headed configuration provides an opportunity to reduce the
chemical injection solution's footprint and optimize efficiency by utilizing a single motor for
twice the injection capability. Flow efficiency is further maximized by bubble-tight check valves.
CheckPoint engineers designed this pump with field efficiency in mind. The included stand ensures that
the pump can be easily placed directly onto the ground or over existing tank containment basins;
however, in the event that the stand is not needed, it can be easily removed and stored. Together, the
Series ATP and its stand provide a quality, effective, and convenient chemical injection solution for a wide
variety of applications.
Description
CheckPoint’s positive displacement, reciprocating chemical injection pumps are specifically designed for,
and extensively proven in, demanding oil and gas production applications worldwide. Our pumps are
utilized in various industries, such as pulp, water treatment, fertilizer dosing, paper, and fluid processing
applications, where precise delivery is operationally paramount. The pneumatic motor, composed entirely
316 SS, remains isolated from the wet end and is dependably able to run on pressurized gas or liquid without
stalling. CheckPoint’s double-acting design eliminates a return spring, which greatly increases repeatability
and reliability over time.
The Series 1250 pump delivers up to 8.0 USG/H (30.38 L/H) and can reliably inject into pressures up to
12,000 PSIG (827 BARG). CheckPoint’s modularly designed chemical heads and range of plunger sizes meet
a wide variety of injection applications. Our pumps maintain unparalleled chemical resistance due to the
essential integration of high-quality, proprietary seal materials. In order to meet a wide variety of chemical
compatibility needs, wetted parts are available in an array of materials, such as 316 SS, Hastelloy C-276,
Duplex 2205, Super Duplex 2507, PVC, ceramic and titanium, and seals are available in Viton, HNBR, FKM,
and FFKM. All construction materials are compatible with sour gas according to NACE MRO175 and ISO
15156.
Only CheckPoint’s pneumatic pumps can recover exhaust gas under significant backpressure. This unique
gas recovery system enables processes to reuse drive gas after it has powered the pump. Consider the environmental benefits, as well as the cost savings, achieved by rerouting spent drive gas to the suction side
of a gas compressor. This exclusive feature aids in lowering gas emissions while powering thermoelectric
generators, feeding catalytic heaters, and even running within enclosures while venting externally
and extensively proven in, demanding oil and gas production applications worldwide. Our pumps are
utilized in various industries, such as pulp, water treatment, fertilizer dosing, paper, and fluid processing
applications, where precise delivery is operationally paramount. The pneumatic motor, composed entirely
316 SS, remains isolated from the wet end and is dependably able to run on pressurized gas or liquid without
stalling. CheckPoint’s double-acting design eliminates a return spring, which greatly increases repeatability
and reliability over time.
The Series 1250 pump delivers up to 8.0 USG/H (30.38 L/H) and can reliably inject into pressures up to
12,000 PSIG (827 BARG). CheckPoint’s modularly designed chemical heads and range of plunger sizes meet
a wide variety of injection applications. Our pumps maintain unparalleled chemical resistance due to the
essential integration of high-quality, proprietary seal materials. In order to meet a wide variety of chemical
compatibility needs, wetted parts are available in an array of materials, such as 316 SS, Hastelloy C-276,
Duplex 2205, Super Duplex 2507, PVC, ceramic and titanium, and seals are available in Viton, HNBR, FKM,
and FFKM. All construction materials are compatible with sour gas according to NACE MRO175 and ISO
15156.
Only CheckPoint’s pneumatic pumps can recover exhaust gas under significant backpressure. This unique
gas recovery system enables processes to reuse drive gas after it has powered the pump. Consider the environmental benefits, as well as the cost savings, achieved by rerouting spent drive gas to the suction side
of a gas compressor. This exclusive feature aids in lowering gas emissions while powering thermoelectric
generators, feeding catalytic heaters, and even running within enclosures while venting externally

Share
Recent Chats
Share via email
Future: handle WhatsApp here
Future: handle LinkedIn here
Future: handle Twitter here
SUBMENU HERE
Share via Chat
Copy Link