See us at MRO Asia Pacific 2025
Opinion: Labor, Not Trade, Must Be Aerospaces Top Concern
Details
More Products & Services
Products & Services
Home - Aviation Group Marketing
Aviation Week Network
120 data points on over 156,000 commercial and business aviation aircraft, including military transports. Discover the most trustworthy resource for the complete aircraft history, plus ad hoc reports, month-over-month trend analysis and details on expected deliveries through 2050.
Aerospace | Aviation Week Network
Aviation Week Network
https://aviationweek.com/themes/custom/particle/dist/app-drupal/assets/awn-logo.svg
People
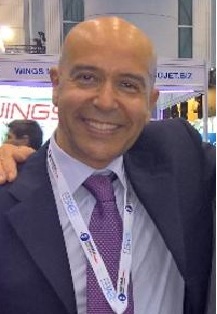
Andrea Rossi Prudente
Aviation Week Network
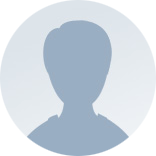
Anthony Lim
Aviation Week Network
Sales director
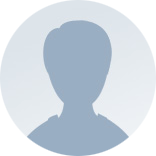
Becca Balmes
Aviation Week Network
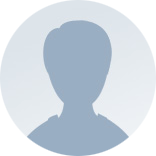
Belinda Tan
Aviation Week Network
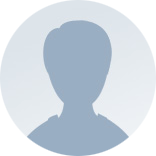
Brian Everstine
Aviation Week Network
Editor
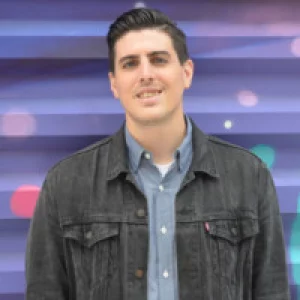
Eddie Krankowski
Aviation Week Network
Assistant Manager, Tradeshows
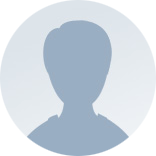
erving dockery
Aviation Week Network
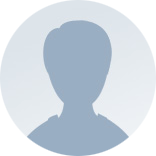
Lisa Tan
Aviation Week Network
Senior Marketing Manager
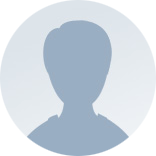
Mark Thomas
Aviation Week Network
Description
The turmoil over tariffs that has engulfed global trade brings with it a little-discussed risk for the aerospace industry that could have a far more lasting impact than inflationary pressures or supply chain disruptions: failure to focus on the sector's production crisis.
This isn't a crisis of demand. Customers desperately want their aircraft. The lack of supply has caused significant financial distress for Southwest Airlines, Ryanair and Wizz Air, to name a few. One of the main causes of aircraft-makers' inability to deliver their products is a labor and skill shortage. This crisis in the commercial aerospace industry is unlike any it has faced. Other crises were ones of demand. The only way out of this crisis of supply is to expand, not cut. The supply chain needs to adapt and grow.
Prior to the COVID-19 pandemic, the aerospace labor force was already aging. At Boeing, the average mechanic had more than 20 years of experience and was about 57 years old. It was not much different at Airbus, where mechanics averaged about 18 years of experience and 46 years of age. Since the pandemic, these demographics have shifted markedly. More than 40% of staff at Boeing now have spent less than five years on the job. The average experience level of Boeing engineers has dropped from nearly 17 years to 12.6 years. For Airbus mechanics, the average is down to 14 years. The picture at their suppliers is no better.
Because less experienced workers are not as skilled as the senior ones they replaced, productivity has eroded. To maintain the same level of output, workforces need to grow to compensate for the lower efficiency.
But that is not trivial. A worker needs about 12-18 months just to become qualified. It takes another two years or so to be truly proficient. This means that a snapshot of the labor force is a look in the rearview mirror. A company's workforce is dependent on hiring or firing practices of the past, especially in the highly skilled industries. That makes employee retention crucial. It is far easier and cheaper to retain good staff than to hire, train and qualify new workers.
The only way for the aerospace industry to fix its production troubles is to expand its workforce. Demand has rebounded sharply from the 2020 pandemic lows, but the industry has meanwhile suffered a huge brain drain at the prime contractor and supplier level. Companies simply need to invest more in talent development, training and upskilling existing workers while bringing on more staff.
Like the products the aerospace industry devises, its workforce is a complicated system that requires sophisticated solutions. A complex business, highly regulated and extremely sensitive to quality, needs to have a deep ecosystem supporting its labor market.
Boeing showed us how long it can take to establish a solid workforce footing. The company decided to create such a system in North Charleston, South Carolina, when it branched out aircraft production there, and it is still working on it more than 20 years on. Spirit AeroSystems' struggles in Kinston, North Carolina, also have roots in immaturity of the workforce. Part of the agreement Boeing struck with its machinist union last year, promising to build the next airplane in Puget Sound, was a nod to this reality.
Labor can function like an ecosystem that, once established, is a treasure for a region. It is mutually beneficial for equipment-makers and suppliers in an area that boosts the local economy, creating other businesses and innovations that generate wider wealth creation. We see this in various aerospace clusters in Seattle, Southern California, Wichita, Montreal and Hamburg, Germany. They have been in existence for more than a century in some cases and have delivered lasting returns.
Without doubt, modern workforces have new demands: flexible schedules, hybrid work arrangements and pay and benefits expectations. Companies need to adapt to this new labor landscape to attract and retain the best talent.
In this era, when labor is not as fungible as it used to be and employers are competing over talent, businesses need to improve employee training, skills and qualifications dramatically. But regional government and educational institutions also have a role and need to help with pre-employment training to ensure an adequate supply of qualified workers to create new clusters.
Trade disruptions can be ended with the stroke of the pen in the White House by suspending tariffs and reverting to a regime that drove an era of aerospace growth. Overcoming the labor crisis will be a yearslong endeavor by multiple stakeholders to deliver growth.
Erik Zahn is managing director at Volare Consultants. He was senior manager of supply chain strategy for Boeing from 1997 to January 2025.
This isn't a crisis of demand. Customers desperately want their aircraft. The lack of supply has caused significant financial distress for Southwest Airlines, Ryanair and Wizz Air, to name a few. One of the main causes of aircraft-makers' inability to deliver their products is a labor and skill shortage. This crisis in the commercial aerospace industry is unlike any it has faced. Other crises were ones of demand. The only way out of this crisis of supply is to expand, not cut. The supply chain needs to adapt and grow.
Prior to the COVID-19 pandemic, the aerospace labor force was already aging. At Boeing, the average mechanic had more than 20 years of experience and was about 57 years old. It was not much different at Airbus, where mechanics averaged about 18 years of experience and 46 years of age. Since the pandemic, these demographics have shifted markedly. More than 40% of staff at Boeing now have spent less than five years on the job. The average experience level of Boeing engineers has dropped from nearly 17 years to 12.6 years. For Airbus mechanics, the average is down to 14 years. The picture at their suppliers is no better.
Because less experienced workers are not as skilled as the senior ones they replaced, productivity has eroded. To maintain the same level of output, workforces need to grow to compensate for the lower efficiency.
But that is not trivial. A worker needs about 12-18 months just to become qualified. It takes another two years or so to be truly proficient. This means that a snapshot of the labor force is a look in the rearview mirror. A company's workforce is dependent on hiring or firing practices of the past, especially in the highly skilled industries. That makes employee retention crucial. It is far easier and cheaper to retain good staff than to hire, train and qualify new workers.
The only way for the aerospace industry to fix its production troubles is to expand its workforce. Demand has rebounded sharply from the 2020 pandemic lows, but the industry has meanwhile suffered a huge brain drain at the prime contractor and supplier level. Companies simply need to invest more in talent development, training and upskilling existing workers while bringing on more staff.
Like the products the aerospace industry devises, its workforce is a complicated system that requires sophisticated solutions. A complex business, highly regulated and extremely sensitive to quality, needs to have a deep ecosystem supporting its labor market.
Boeing showed us how long it can take to establish a solid workforce footing. The company decided to create such a system in North Charleston, South Carolina, when it branched out aircraft production there, and it is still working on it more than 20 years on. Spirit AeroSystems' struggles in Kinston, North Carolina, also have roots in immaturity of the workforce. Part of the agreement Boeing struck with its machinist union last year, promising to build the next airplane in Puget Sound, was a nod to this reality.
Labor can function like an ecosystem that, once established, is a treasure for a region. It is mutually beneficial for equipment-makers and suppliers in an area that boosts the local economy, creating other businesses and innovations that generate wider wealth creation. We see this in various aerospace clusters in Seattle, Southern California, Wichita, Montreal and Hamburg, Germany. They have been in existence for more than a century in some cases and have delivered lasting returns.
Without doubt, modern workforces have new demands: flexible schedules, hybrid work arrangements and pay and benefits expectations. Companies need to adapt to this new labor landscape to attract and retain the best talent.
In this era, when labor is not as fungible as it used to be and employers are competing over talent, businesses need to improve employee training, skills and qualifications dramatically. But regional government and educational institutions also have a role and need to help with pre-employment training to ensure an adequate supply of qualified workers to create new clusters.
Trade disruptions can be ended with the stroke of the pen in the White House by suspending tariffs and reverting to a regime that drove an era of aerospace growth. Overcoming the labor crisis will be a yearslong endeavor by multiple stakeholders to deliver growth.
Erik Zahn is managing director at Volare Consultants. He was senior manager of supply chain strategy for Boeing from 1997 to January 2025.

Share
Recent Chats
Share via email
Future: handle WhatsApp here
Future: handle LinkedIn here
Future: handle Twitter here
SUBMENU HERE
Share via Chat
Copy Link